Using powder metal to manufacture components can be more cost-effective than other manufacturing methods. However, despite being cost-effective, using powder metals for manufacturing parts is not entirely straightforward. The porosity of the structure must be considered in every aspect of its construction. Even sintering, the most common heat treatment option when working with these materials, is affected by the part’s porosity.
Powder Metal Compaction and Porosity
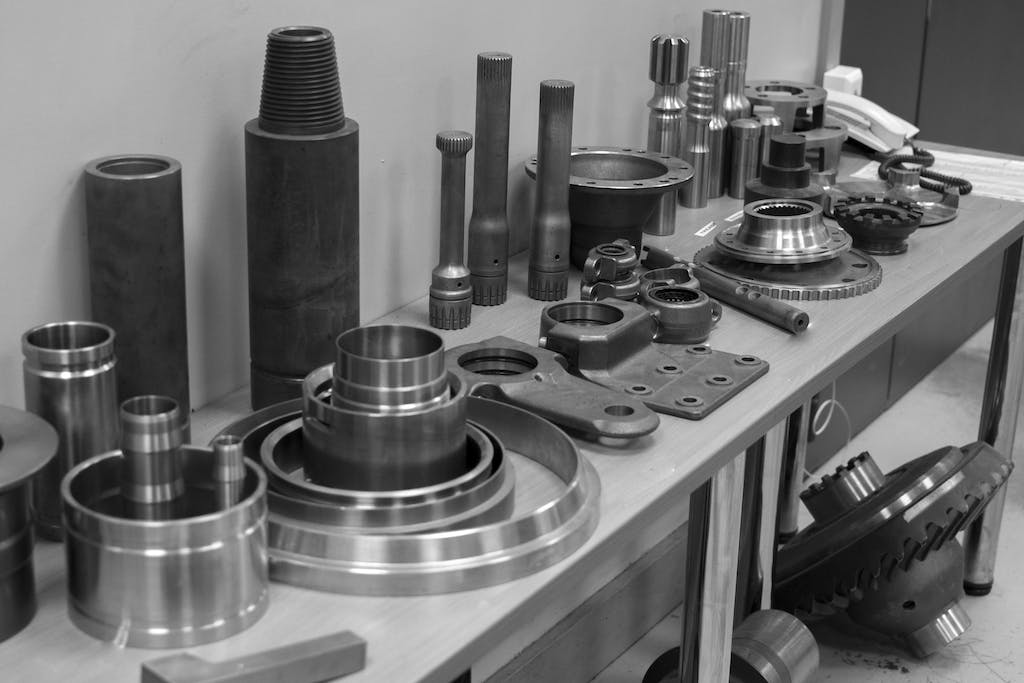
The first step of the manufacturing process involves using a mold to shape the powder metal. The powder is placed in a mold and then compacted to form the shape of the part. Depending on the pressure used for this compaction, the porosity of the piece will differ. Every component made using powder metals will have some level of porosity due to how they are manufactured. Higher pressures lead to a decrease in porosity, which is generally ideal.
However, high-pressure compaction can also cause powder grains to break, deform, or a combination of the two depending on the material being used. Brittle materials tend to break, elemental materials like copper and iron tend to deform, and alloys fall somewhere in between. These breaks and deformations can themselves lead to an unwanted increase in porosity.
Porosity and Hardenability of Powder Metals
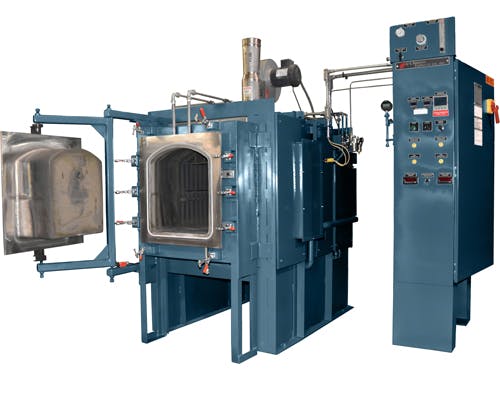
Sintering is the next step of the manufacturing process after compaction. When done right, a part should retain its shape after being compacted. However, it is not hardened enough in this state to be used. That is where sintering comes in. The goal of sintering is to harden the part so that it can withstand surface damage and general external stresses. The sintering process is performed at about 75% of the melting temperature of the primary part material in an atmosphere composed of mostly N2, about 10% H2, and small amounts of CH4. The CH4 is there to bond with the water vapor that is produced so the vapor doesn’t bond with the carbon in the part instead.
When sintering, the porous nature of powder metal parts can make them more difficult to harden than parts manufactured by different means. Reaching the martensite or bainite phase is the goal of hardening. But this can be difficult if the part has high porosity. The air pockets within the part can slow the formation of martensite.
Porosity and Residual Fluids
Residual fluids are another problem for powder metal parts. Fluids can become trapped within the pores of the piece, which can then lead to unwanted damage or hazardous conditions down the line. During sintering, water vapor may become trapped within the part. If this occurs, it can cause internal rusting depending on the metal the part is made out of. And during quenching, the quench media, typically an oil, can also become trapped. If this happens, it can lead to the oil within the part igniting during post-quenching heat treatments such as tempering. It is important to draw these fluids out of the piece before performing additional heat treatments.
However, the ability for porous parts to retain liquid is not always a negative characteristic. Self-lubricated bearings are one type of part that makes use of this ability. A lubricant is housed within the bearing and is excreted from it over time to keep the part lubricated. This is a vital characteristic for parts on which maintenance is unable to be performed, such as within sealed motors and in many aerospace applications.
Post-Quench Tempering of Powder Metal Parts

When tempering a powder metal part after quenching has taken place, residual oil within the part is the primary concern. If there is residual oil inside the pores, it can lead to hazardous fumes, smoke, and fire. But, despite these hazards, tempering is a vital part of the manufacturing process for many powder metal pieces.
While sintering is used to improve the hardness of the piece, tempering is later used to improve the toughness at the expense of hardness. There is generally a tradeoff between toughness and hardness. If a piece has increased hardness, it tends to have decreased toughness. And if it has increased toughness, it tends to have decreased hardness. Which quality is more important will depend on the type of part and the specific situation in which it is going to be used. Hardness is the ability to resist surface damage and is more important for applications involving high surface wear. Toughness is the ability to resist fracturing and is more important for applications in which the part will be exposed to higher pressures and stresses.
Conclusion
The powder metal part manufacturing process begins with the molding and compaction of the powder metal into the shape of the part. During this step of the process, the porosity of the part is determined by the pressure under which it is compacted. That level of porosity is important to keep in mind throughout the rest of the manufacturing process. The next step is to sinter the piece. Sintering increases the hardness of the part but may leave it with residual water vapor inside the pores. Once sintering is complete, the part is quenched in an oil media. If the part is to be tempered after quenching to improve the toughness, the residual oil must first be extracted from the part to prevent a fire from breaking out.
L&L Special Furnace
Manufacturing powder metal parts involves numerous heat treatment processes that require specific machinery to perform. At L&L, we design and manufacture specialty furnaces for all of your heat treatment needs. For sintering, we recommend our XLC, JSC, and TBU furnaces. Contact us today to learn more about our sintering, tempering, and other heat treatment furnaces.