When the goal for a part is the longest possible lifecycle and highest performance while operating under high temperatures, in a corrosive environment, and with the potential for extreme wear, then powder metal manufacturing can offer a very cost-effective option. Not only are the parts strong, robust, and wear-resistant, but the advent of additive manufacturing has made it possible to minimize their weight, maximize their durability, and create parts that are simply impossible to manufacture by conventional manufacturing methods.
What Are Powdered Metals?
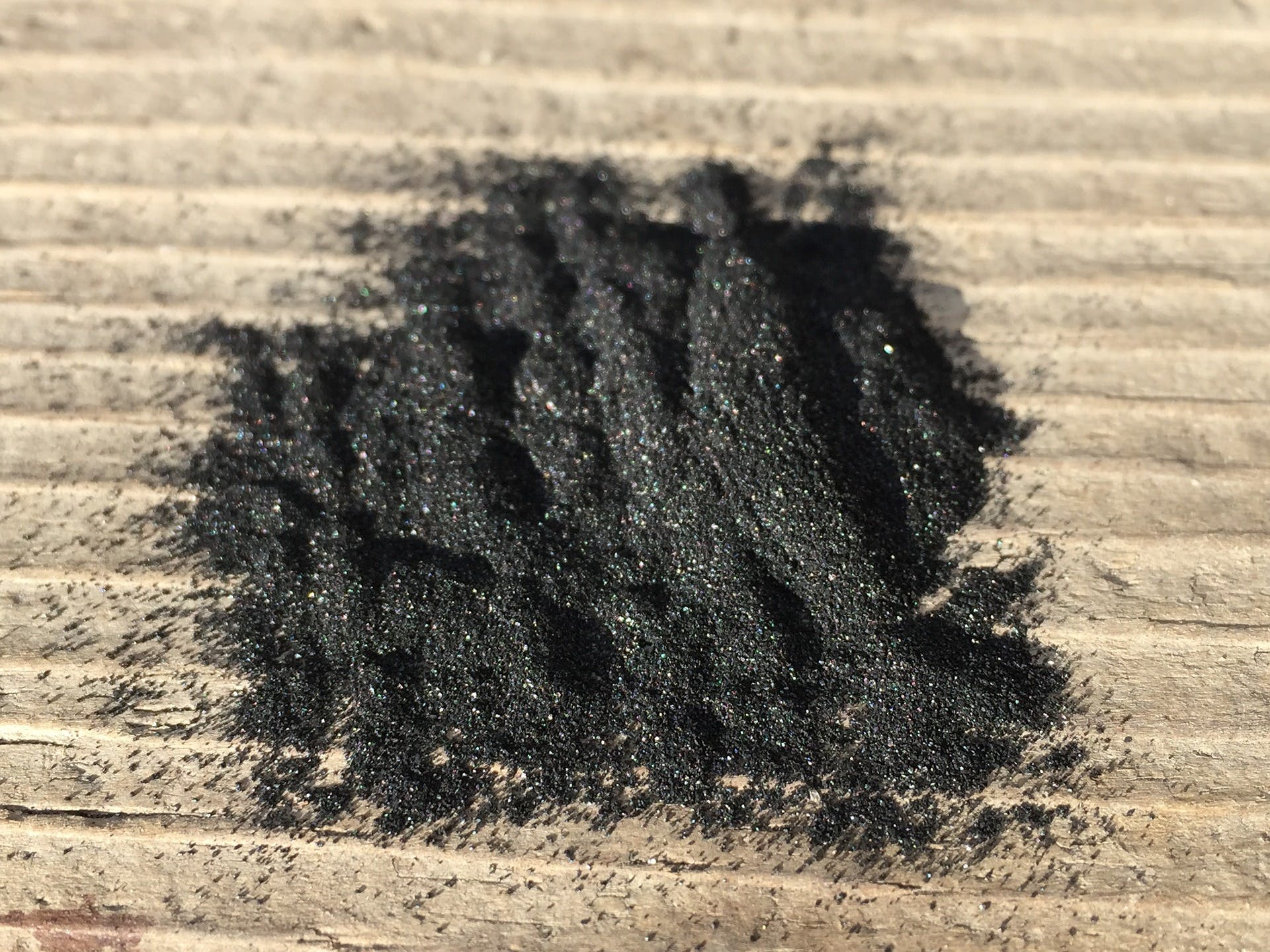
Powder metal (PM) parts are created from a very fine metal powder that is compressed and sintered to achieve its final shape. This is quite different from cast parts, which begin their life as a liquefied metal, or from machine or forged parts, which start off as stock metal. The powder metal manufacturing process makes it possible to create parts with an extremely complex geometry. While such parts might be made through casting or machining, the manufacturing costs increase dramatically as the complexity rises. PM parts, however, are cost effective even when the geometry is complicated and can make parts that are impossible to fabricate using any other methods.
Another key benefit of powder metal is that it is a net or near net manufacturing process that results in minimal waste material. Rather than subtracting geometry and materials in order to create a part, PM does not waste any metal, making it a much more efficient and environmentally sustainable process. Because PM is so closely allied with computer-aided manufacturing, parts can be created to simultaneously optimize weight, strength, stiffness, and hardness. This can be vital for applications in industries such as aerospace where weight must be minimized.
Where Powder Metal Manufacturing Is Used
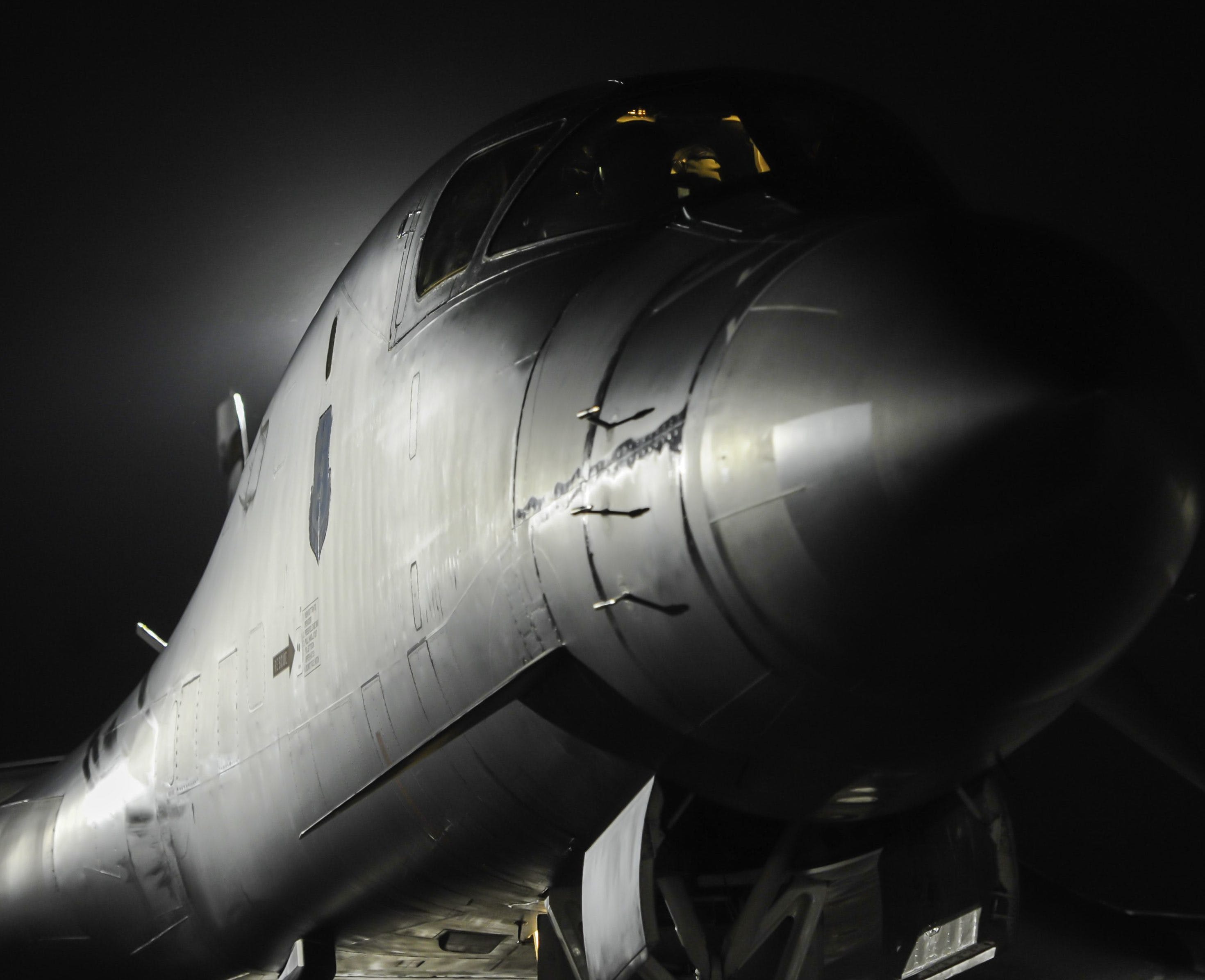
Powder metal products can be found in a wide array of industries, including aerospace, automotive, marine, and biomedical. Many everyday products may have been created via PM, such as light bulb filaments, automotive engine components, the lining of friction brakes, medical devices, and lubricant infiltrated bearings. PM can also be used for more exotic purposes, such as heat shields used on spacecraft during re-entry, electrical contacts for extremely high current flows, and gas filters. The parts produced by PM can be used as prototypes or as fully functional parts. As better methods of manufacturing and heat treatment of PM parts are developed, the applications will continue to grow and PM parts will become even more commonplace.
Background on Powder Metal Technology
Powder metallurgy (which forms the basis of modern PM methods and technology) actually dates to the 1940s. Early products made by these methods include porous bearings, electrical contacts, and cemented carbides. Through the intervening years, companies wisely invested in powder metallurgy technology and advances, focusing their research on aspects such as refinement, new alloy development, and atomization techniques for efficiently generating fine powders. Such research and innovation continue to this day. One of the most groundbreaking developments is net shape production of PM parts via additive manufacturing (AM).
Metals Used in Powder Metallurgy Processes
The most commonly used base metals for PM processes include alloyed metals such as:

- Iron
- Steel
- Copper
- Stainless steel
- Titanium
- Aluminum
- Tin
- Molybdenum
- Tungsten
- Tungsten carbide
- Various precious metals
Most industrial PM products are comprised primarily of iron and steel along with other elements, including both metal, semi-metal, and transitional elements. Different alloying elements can be added to the base metals to achieve customized or improved material properties.
Basics of the Powder Metal Manufacturing Process
Typical PM parts are made in three basic steps: the blending of the metal powder (pulverization), die compaction, and sintering of the product. Additional heat treatment steps may be required after sintering in order to achieve the appropriate density, dimensions, and surface finish.
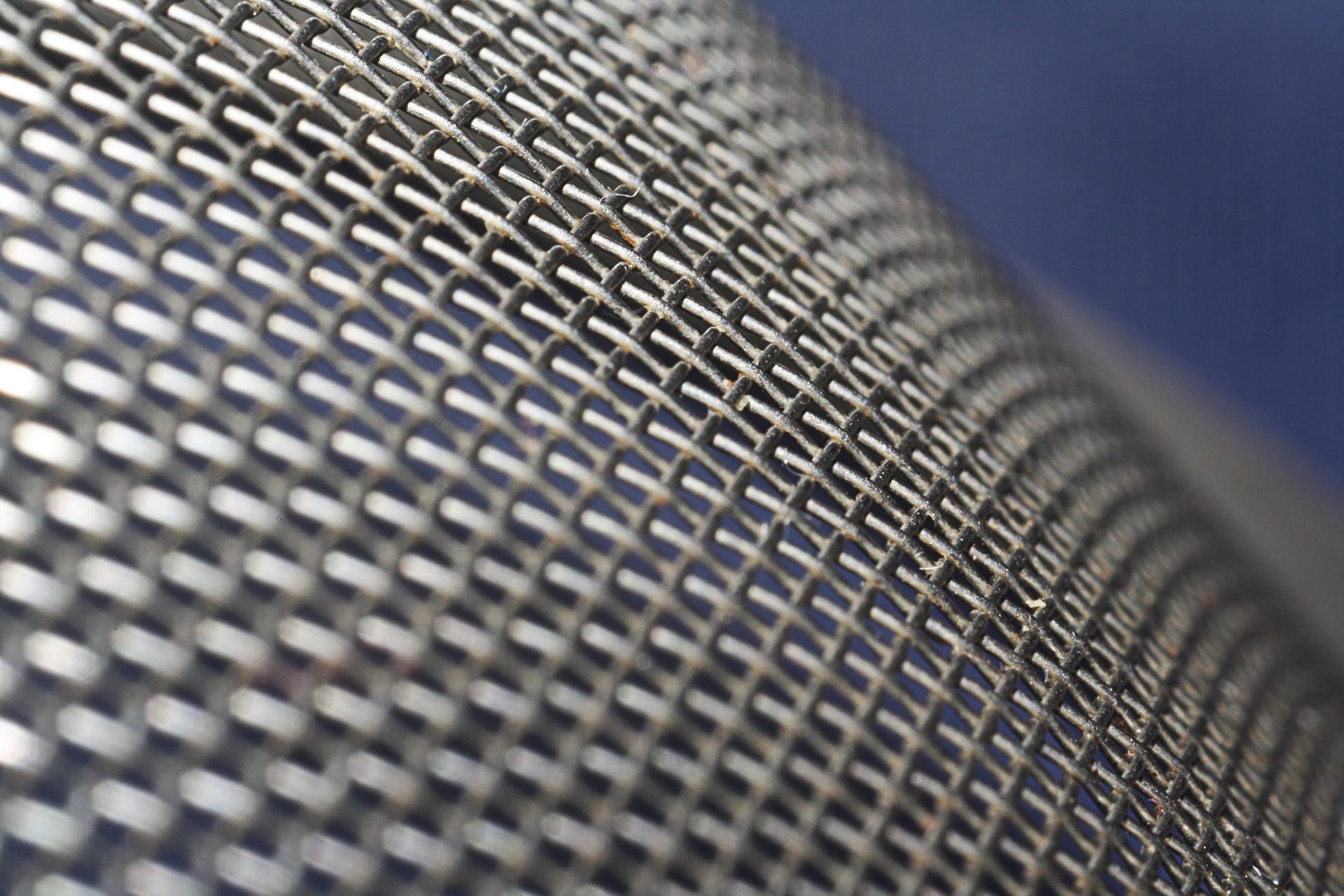
Pulverization and sieving prepare the metal powders for use in PM. The powders can vary in both shape (some are designed to be spherical) and size. Metallic powders can be produced through one of several different processes, including grinding, crushing, electrolytic deposition, chemical reactions, and atomization. The size and shape of the particles is an important factor when designing a part for manufacturing by PM methods.
Die compaction is accomplished using a pre-determined amount of pressure in relation to the part. This pressure is applied at room temperature, while sintering then begins at elevated temperatures conducted at atmospheric pressure. Note that sintering is performed under strict atmosphere-controlled conditions. After sintering, secondary heat processes are often used to enhance mechanical properties and dimensional precision.
How Powdered Metal Parts are Formed
One of the oldest methods to make PM parts is still used today – in fact, it is used to manufacture 1MT/year of iron-based alloy structural components. These components are made by blending a fine iron metal (typically <180 microns) with additives such as carbon, copper, and/or nickel and wax lubricant. The wax lubricant facilitates pressing the powdered metal into a die of the desired part shape.
This “green” part is then heated in a highly controlled atmosphere in a metallurgical furnace. This allows the compacted powdered metal to bond via the sintering process. The part produced after sintering is close to the finished part but still contains between 5-15% porosity and is thus weaker than a finished product resulting in sub wrought steel properties.
Traditional PM Processes
There are many other PM processes that have been successfully developed since the 1940s. The more traditional processes include powder forging, hot isostatic pressing (HIP), metal injection molding, and electric current assisted sintering.
In powder forging, a pre-form is made using the conventional press and sinter methods, but the part is then heated and hot forged. The result is a full-density part with as-wrought properties.
In HIP, the powder is gas atomized and spherical in shape. The mold used is typically a metal can of appropriate shape into which the powder is added. The mold is sealed, vibrated, and then all air is vacuumed out via a pump. The mold is then placed into a hot isostatic press where it is heated to a homologous temperature and its internal pressure is increased via external gas pressure. This particular PM process results in a finished part that has the correct shape and full density. The part has as-wrought or better mechanical properties.
Hot isostatic pressing was developed in the late 1950s and early 1960s and entered tonnage production in the 1970s. In 2015, HIP was used to manufacture approximately 25,000 tons of stainless steel and tools steels annually. This, in turn, lead to the manufacture of super alloys used in aerospace and jet engines.
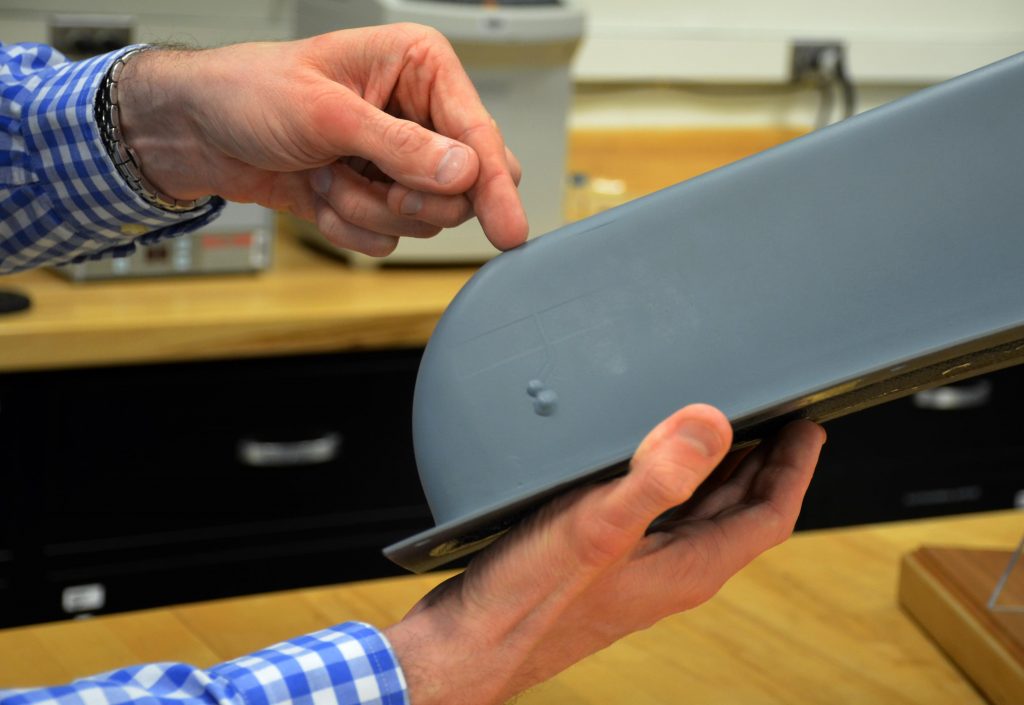
Another common manufacturing technique for PMs is metal injection molding (MIM). During this process, spherical metal powder that is less than 25 microns in size is mixed with either plastic or wax as a binding agent. Once a near solid part has been formed (65% volume), it is injection-molded. The result is a “green” part that typically has a very complex geometry. The green part is then heated under controlled conditions to remove the binder in a process known as de-bindering. The part at this stage is referred to as a “brown” part, but the process is still not complete. The brown part is then subject to an atmospherically controlled sintering process. The part’s volume is reduced by about 18%, and the final part is extremely dense at 97-99%.
Electric current assisted sintering (ECAS) is a different type of powder metal manufacturing process that makes extensive use of electric currents and does not require the use of binders. Instead of de-binding or sintering after pressing, electric currents are used to increase the density of the powder, which significantly reduces the thermal cycle needed to maintain the strength and density of the final part. This in turn reduces the overall production time for the part. For example, some parts will see a process time reduction from 15 minutes down to just a few microseconds. However, this process only works on relatively simple shapes. Another interesting aspect of the ECAS process is that the molds used are actually designed for the final part shape because the powders achieve final density while filling the mold under pressure and heat. This takes care of both distortion and shape variation.
Introduction to Additive Manufacturing/Metal 3D Printing
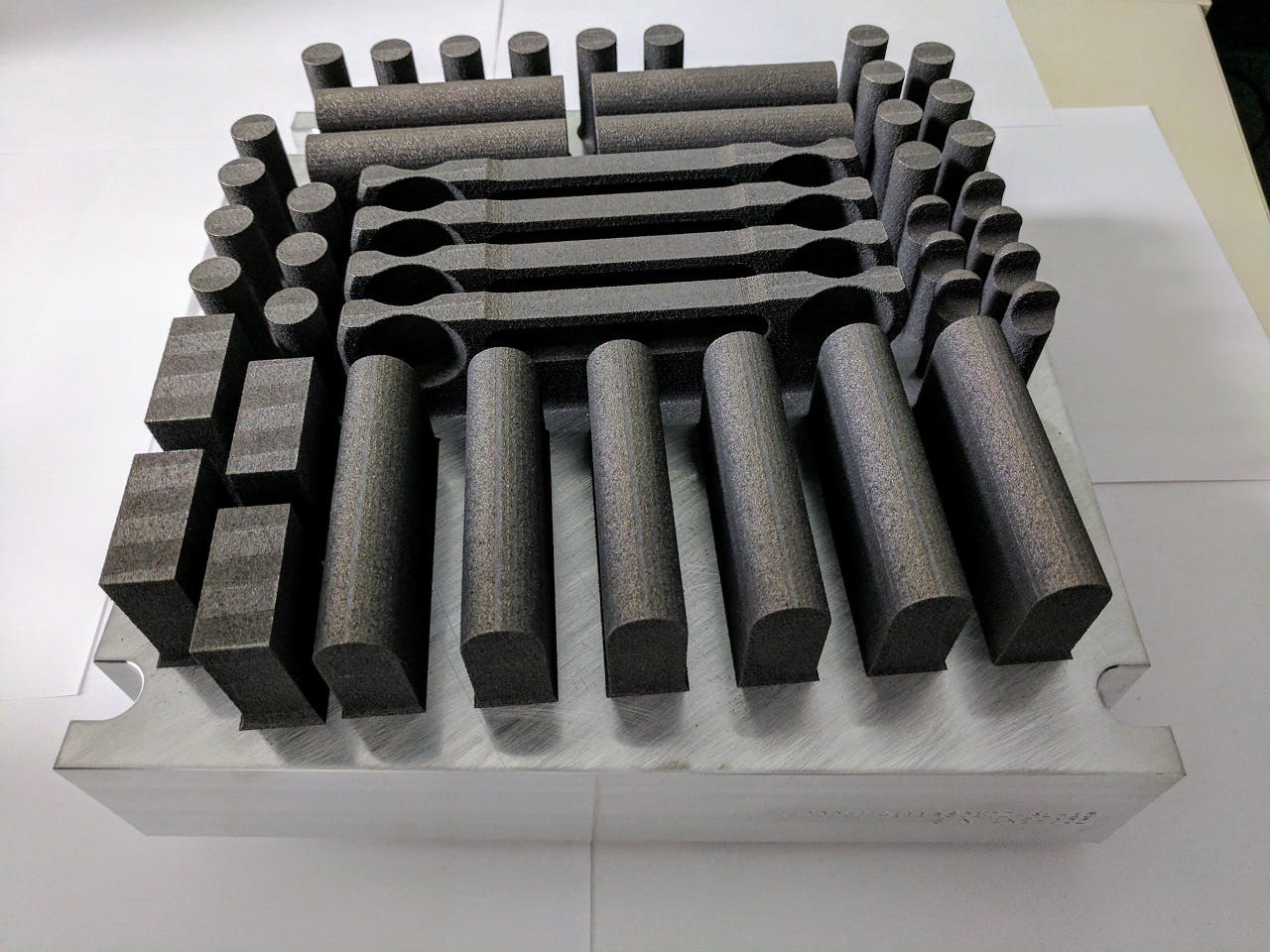
Additive manufacturing (AM), sometimes called metal 3D printing, is considered a newer PM method, although its history dates back to the 1980s. In this method, parts are formed by melting or laser sintering metal powders (as well as other forms of metals, ceramics, and polymers) and additives. What makes these two methods so different from the other PM methods is the layer-by-layer approach taken to build up the part (hence the term additive manufacturing, which refers to the process of adding a layer at a time to form the part). This allows parts to be built a single layer (micrometers thick) at a time based directly on 3D digital models of the part via computer aided manufacturing (CAM). This layered approach is digitally controlled to achieve a high level of precision.
AM supports the manufacturing of very intricate, complex geometries that are often impossible to create using other methods such as metal casting or machining. AM is known for being a highly customizable, versatile, flexible design process that supports not just metals but hybrids, composites, and even functionally graded materials (FGM). Materials that can be used include hybrids and composites, metals, polymers, nanomaterials, pharmaceuticals, biological materials, and ceramics.
Applications of AM
AM is excellent for the production of prototypes for a variety of industries, including aerospace, medical, and automotive. It has also found extensive use in connection with rapid tooling. Parts manufactured by metal 3D printing are used in in everything from nuclear to gas turbines to marine applications.
As for how reliable the final parts are, consider the following:
- Human use devices manufactured by AM have been approved by the FDA
- Major automobile manufacturers are using AM to manufacture engine components for use in on-road vehicles (i.e., not just in laboratory testing)
- The International Space Station has been equipped with an AM machine
AM Methods
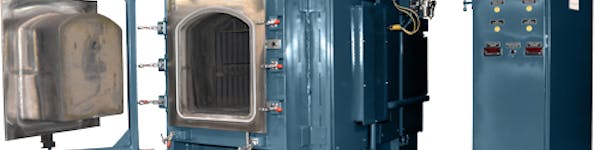
L&L’s XLC series furnace for powdered metals debindering and sintering
The two most popular AM methods at the moment are Electron Beam Manufacturing (EBM) and Direct Metal Laser Sintering (DMLS). For each layer of the part, a layer of extremely fine metal powder, droplets, sheet, or wire is deposited and then melted by the laser beam. Both use focused heat for the sintering/de-bindering process.
In EBM, an electron beam provides the heat for welding the metal powder together, layer by layer. Oxidation is avoided because the process takes place in a vacuum. In DMLS, as the name implies, a laser beam provides the heat needed in an atmosphere of clean argon, which also prevents oxidation. Unlike conventional machining, DMLS can create enclosed spaces. Both EBM and DMLS can create parts with incredible tolerances and precision. For AM parts that are intended for critical applications, a HIP treatment is often needed in order to achieve the desired density for the final part.
Heat Treatment of PM Parts
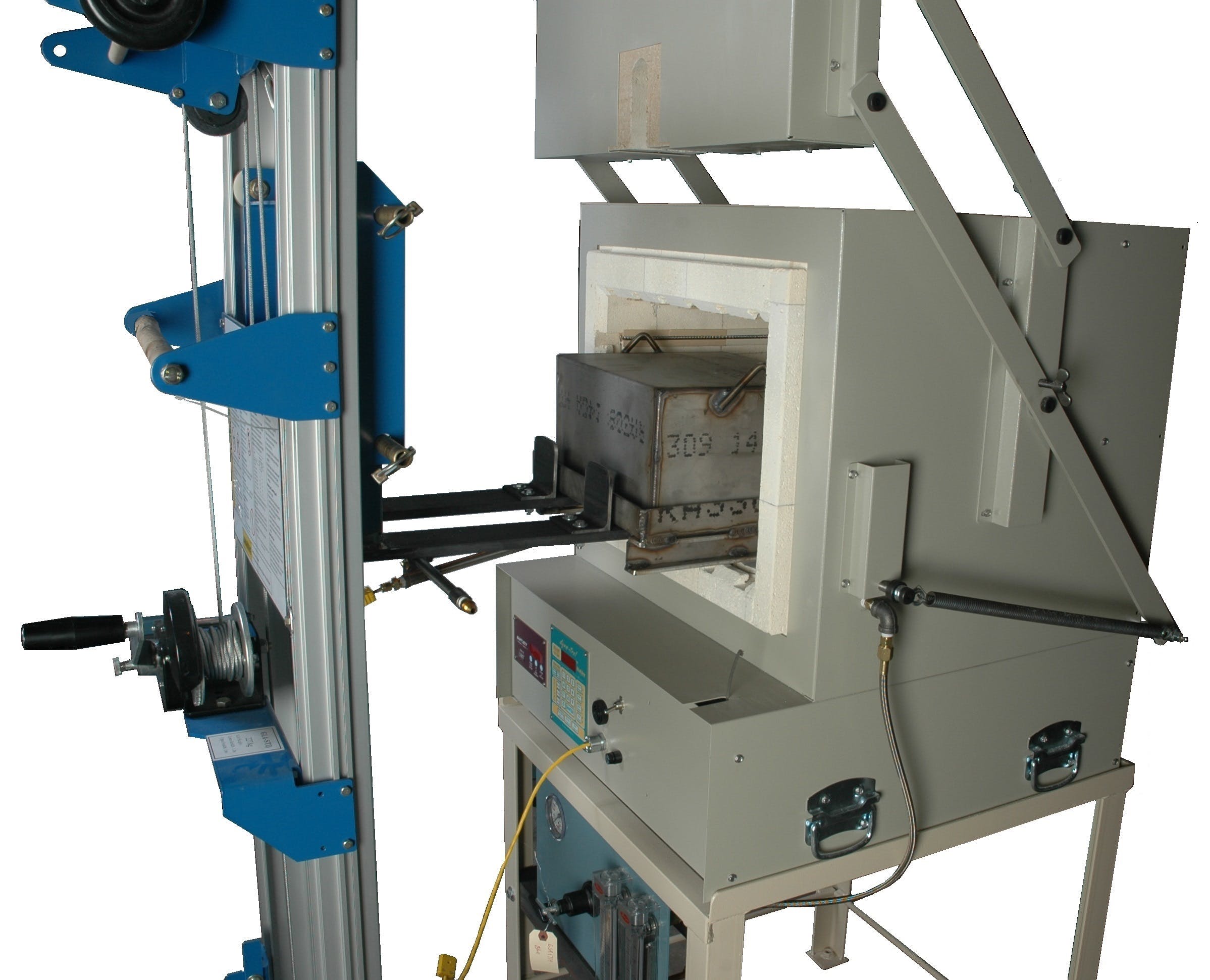
L&L’s GSR1714 with removable retort for inert atmosphere use
DMLS and most other PM processes involve a subsequent heat treatment step. The purpose of heat treatment is to control mechanical properties of the final part, such as strength and surface hardness. The majority of PM heat treatments require precise temperature control and consistency in an inert atmosphere. The purpose of an inert atmosphere is to avoid the threat of oxygen molecules contaminating the sintered part. If the part is contaminated, it will affect the porosity of the final part which in turn has a negative impact on both the mechanical and chemical properties achieved. The most common inert atmospheres used are nitrogen, argon, and hydrogen.
The first heat treatment process that almost all PM parts are exposed to is sintering. The most common furnace atmosphere for the sintering step is nitrogen with 10% hydrogen. To prevent decarburization, a small amount of methane gas may also be added.
One of the more common PM heat treatments is sinter hardening. Sinter hardening is used to increase the surface hardness of the part and it requires a carbon-controlled atmosphere and highly controlled temperatures. Unlike traditional hardening methods, there is a significant reduction in part distortion because the quench is far less severe. Typical atmosphere choices include ammonia/nitrogen or hydrogen/nitrogen with a small amount of hydrocarbon gases. Other hardening and quenching treatments may use nitrogen/methonal.
Tempering is another typical PM heat treatment process. Tempering allows the microstructure to be modified in order to increase the toughness of the part. There are different types of tempering, including martempering and austenizing.
Some AM parts require an additional HIP treatment, as discussed earlier. The HIP treatment takes place in a pressure vessel filled with argon gas. HIP takes place subsequent to stress-relieving.
Atmospheres Used with PM/AM Heat Treatment
Sintering, tempering, hardening, and HIP treatments require special atmospheres. These most common atmospheres required nitrogen, argon, and hydrogen. The quality of the final part depends heavily on the purity and control of the atmosphere during sintering and subsequent heat treatments. Note that some PM processes and heat treatments may even require a vacuum.
L&L Special Furnace Solutions for Powder Metal Manufacturing
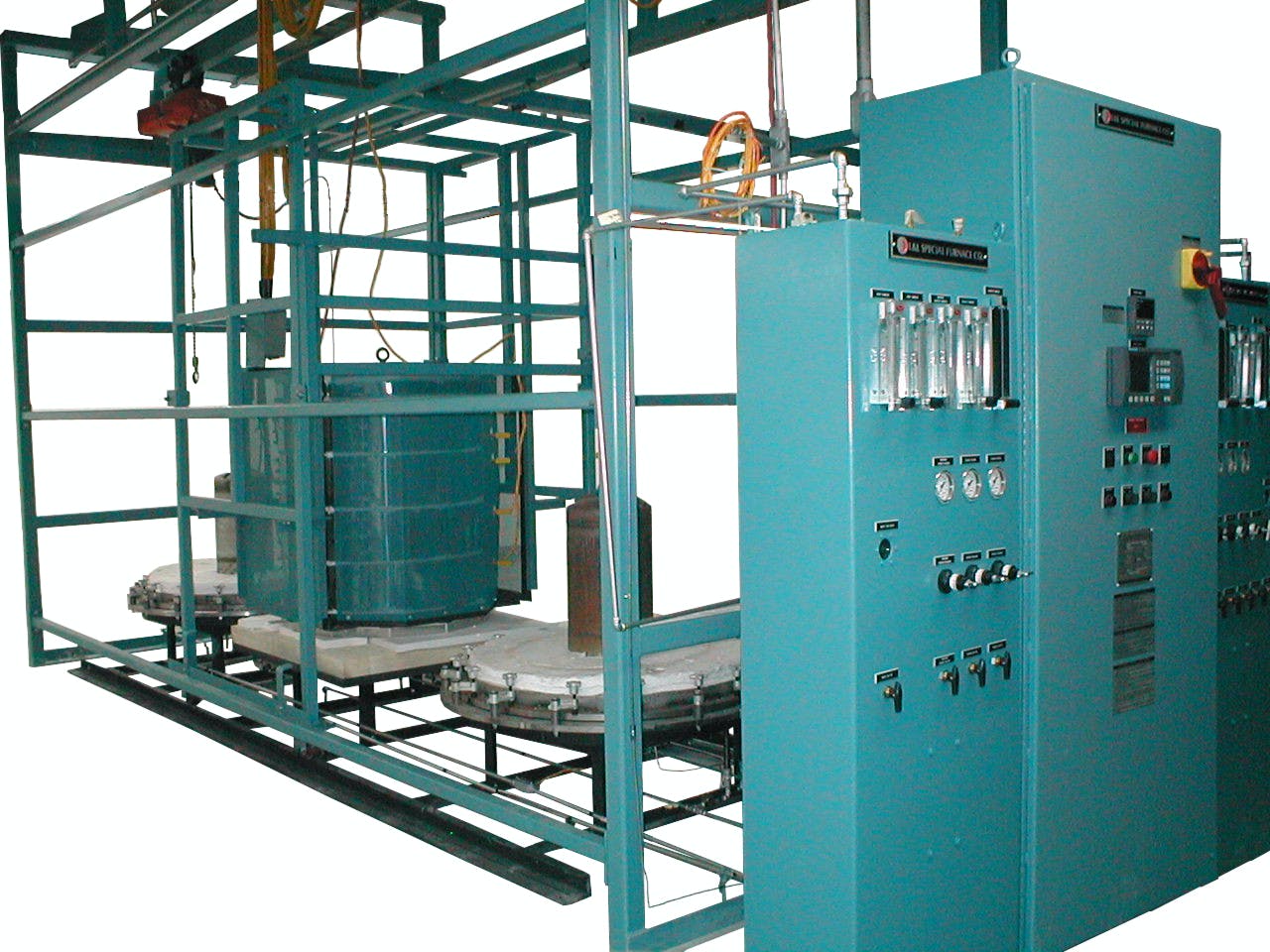
JSC1012 oven for powdered metals
At L&L Special Furnace Co., Inc. we recognize the evolving needs of powder metal manufacturing and additive manufacturing, and we make sure that we can offer the furnaces and heat treatment ovens to meet those needs. All of our products are known for their precision control systems, uniform heating and temperature distribution, and incredible value. We’ve aligned our product offerings so that they are highly customizable to meet our customers’ heat treatment needs. L&L Furnace also offers setup services to assist our customers in implementing their equipment as quickly as possible and repair services to help get systems back online in the unlikely event that a repair is needed.
For AM and PM heat treatments, we provide several different options. For example, the GS1714 supports an inert air environment and offers powerful multi-program control and even heating. It is ideal for applications including powder metals and ceramics. These furnaces are kept in stock and ready for immediate shipment.
Atmospheric retort furnaces, like those in our electric-powered XLC series, work extremely well for PM and AM applications. These furnaces provide a highly stable atmosphere, and the control system, alloy retort, and flow system are completely integrated as one unified array.
The JSC Series is 2200°F hydrogen atmosphere-controlled shuttle lift retort furnace with a bell-type “top hat” alloy low dew point retort. Any application that requires purely inert atmospheres (including 100% hydrogen or hydrogen mixtures) can be used in the JSC series of furnaces.
Our reputation for quality and value has enabled us to provide industrial ovens, furnaces, and quench tanks to customers in industries such as aerospace and medical equipment manufacturing – industries where precision, quality, and reliability are critical. Contact us today to find the heat treatment solutions and customer service excellence that you need!