Motor laminations are thin metal sheets that are stacked together to create the core of an electric motor’s stator and rotor. Components that are to be used in the aerospace industry must be manufactured to precise specifications with specific mechanical properties. Motor laminations are no exception, as they are some of the most important individual components for the proper operation of aircraft. To achieve the specifications and properties needed, motor laminations undergo an annealing heat treatment within a hydrogen atmosphere.
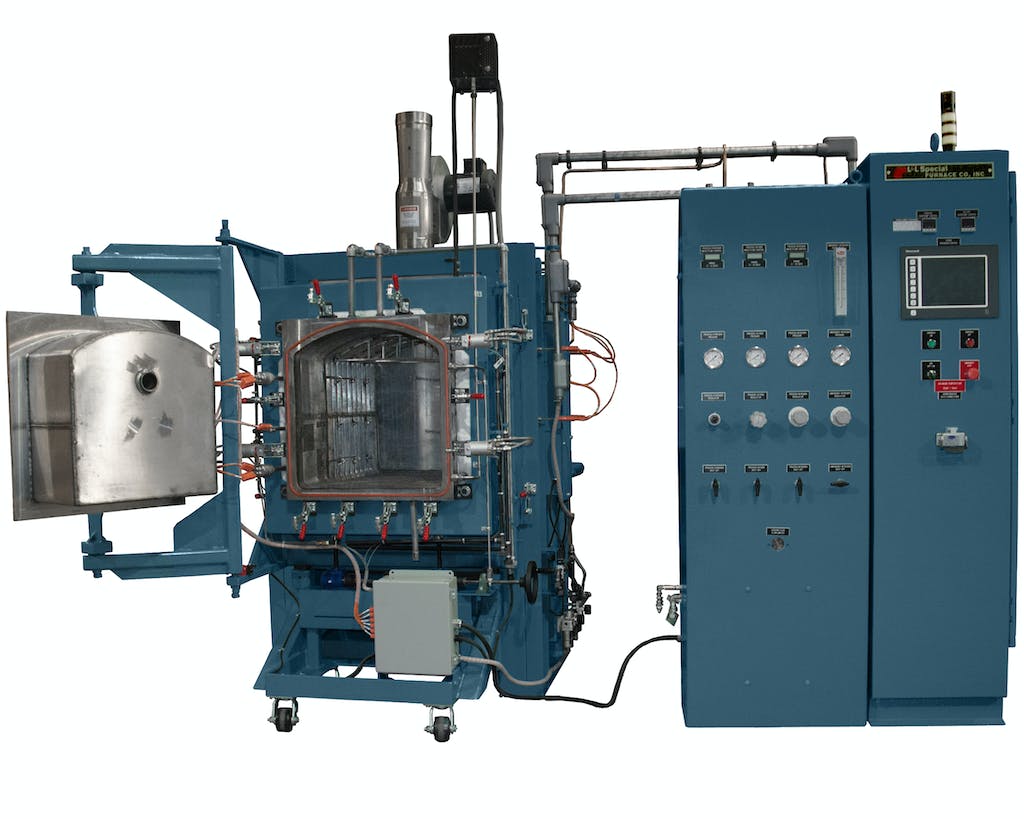
Press Release: Electrical Box Retort Furnace for Annealing Motor Laminations in Hydrogen
L&L Special Furnace Co. has shipped a retort furnace to a northeastern US manufacturer of motor laminations.
Annealing Motor Laminations
Annealing is used to provide silicon steel laminations with additional beneficial properties. Some of these properties are beneficial for the conditions the final product is going to be working in. Other properties are beneficial if any additional treatment, working, or machining needs to be performed on the laminations before they are fused together into a core. And, annealing can even be used to remove or reduce negative characteristics left over from previous treatment.
Benefits of Annealing
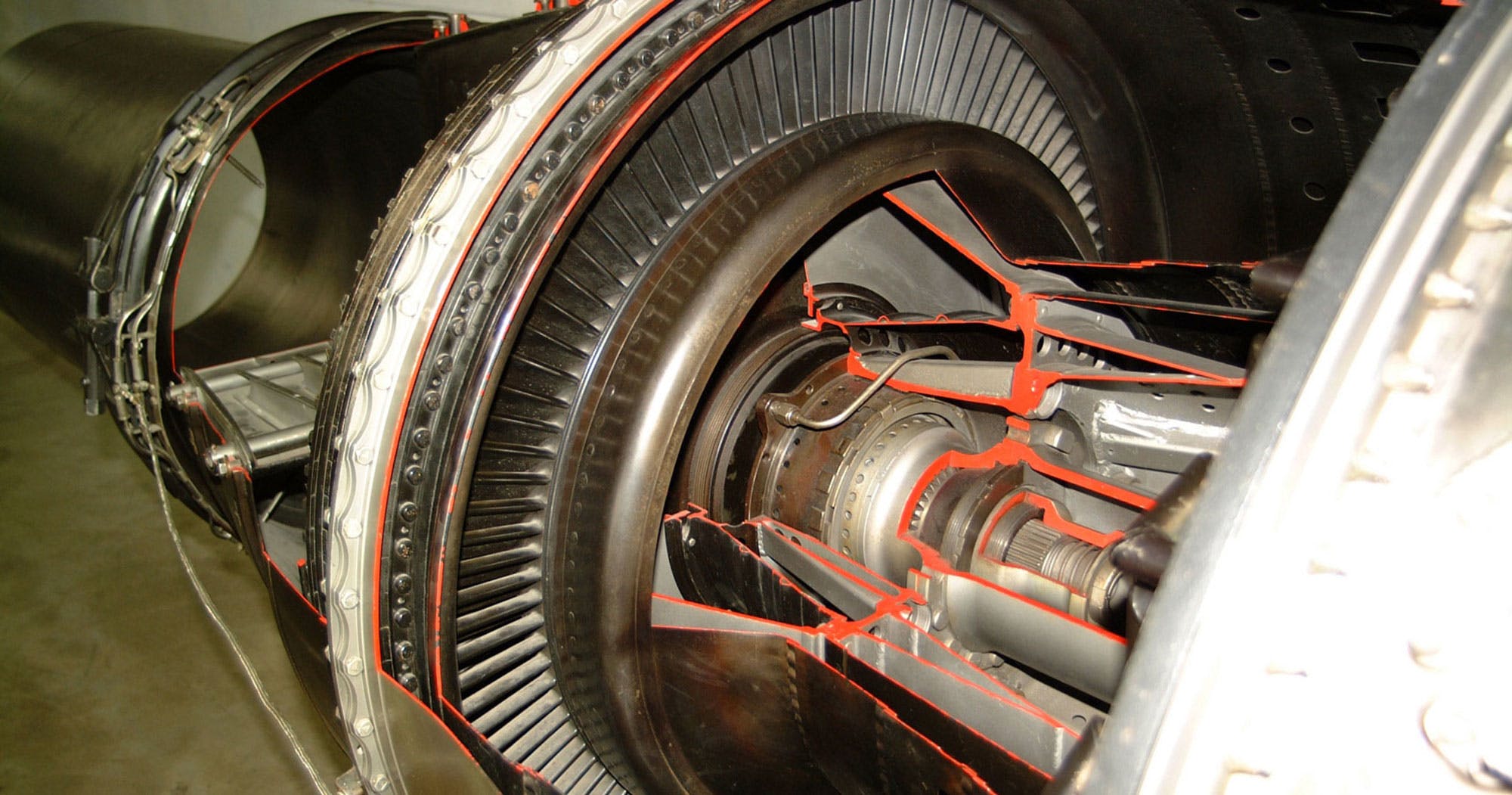
Starting with the improvements of positive material characteristics, annealing improves the appearance, ductility, grain size, magnetic properties, permeability, strength, structure, and toughness. The common thread between these characteristics is that they all increase the durability or electromagnetic attributes of the part, which are both vital for electric motor laminations. Electric motors must be able to withstand frequent and continuous use without wearing out or becoming less efficient over time.
Negative characteristics that can be reduced or removed through annealing include excess hardness and brittleness, built-up stresses, and core loss. While hardness is a beneficial quality for many components, excess hardness can lead to parts becoming brittle and easily broken. The last things you want inside an electric motor are metal shards from broken laminations. Relieving built-up stresses from prior working and machining will also help the components withstand their work environments better. And decreasing core loss improves the electromagnetic attributes of the part.
Stages of Annealing
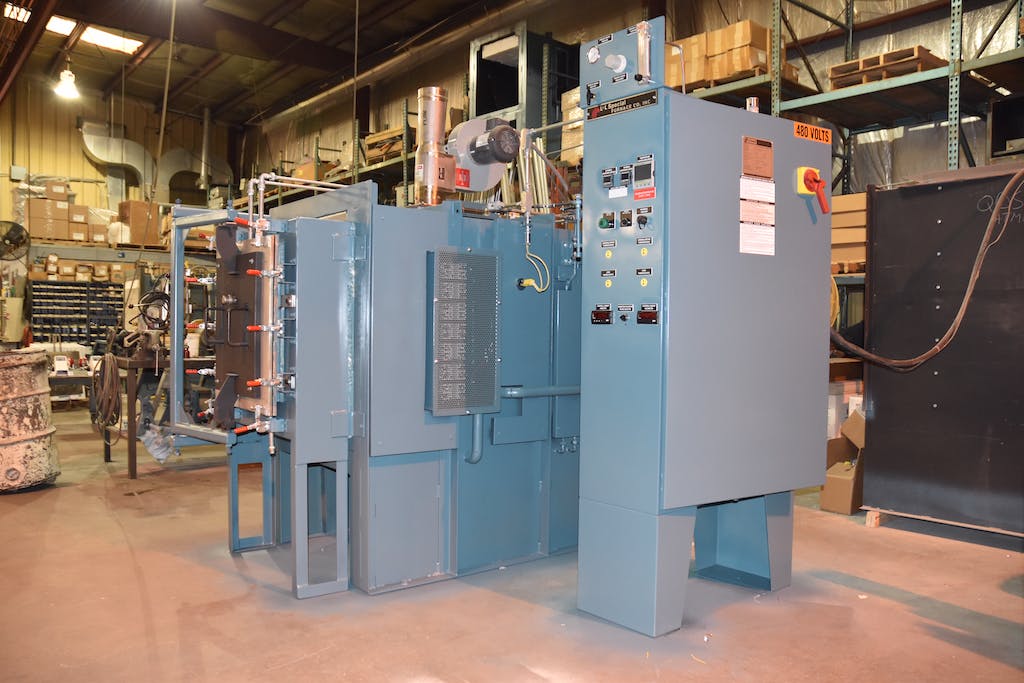
The three stages of annealing are recovery, recrystallization, and grain growth. Recovery is the stage in which the internal stresses of the part are relieved. As parts are formed, worked, and machined, they build up internal stresses that can eventually lead to part failure. These built-up stresses within the part are reset during the recovery stage so it can undergo further working after it has been annealed. Recovery is performed at a temperature below the recrystallization temperature for the material.
Recrystallization is done above the recrystallization temperature for the material, but below the melting temperature. The recovery stage relieves stresses by resetting the distorted grains within the material. In the recrystallization stage, new grains are formed that do not have stresses carried over from previous work done on the part.
The final stage of annealing is the grain growth stage. As the name implies, this is when the newly formed grains from the recrystallization stage are locked in as the new microstructure of the part. It is done by continuing to heat the part after recrystallization is complete. Grain growth is the stage during which the material’s ductility is increased and its hardness is decreased.
Why Use a Hydrogen Atmosphere
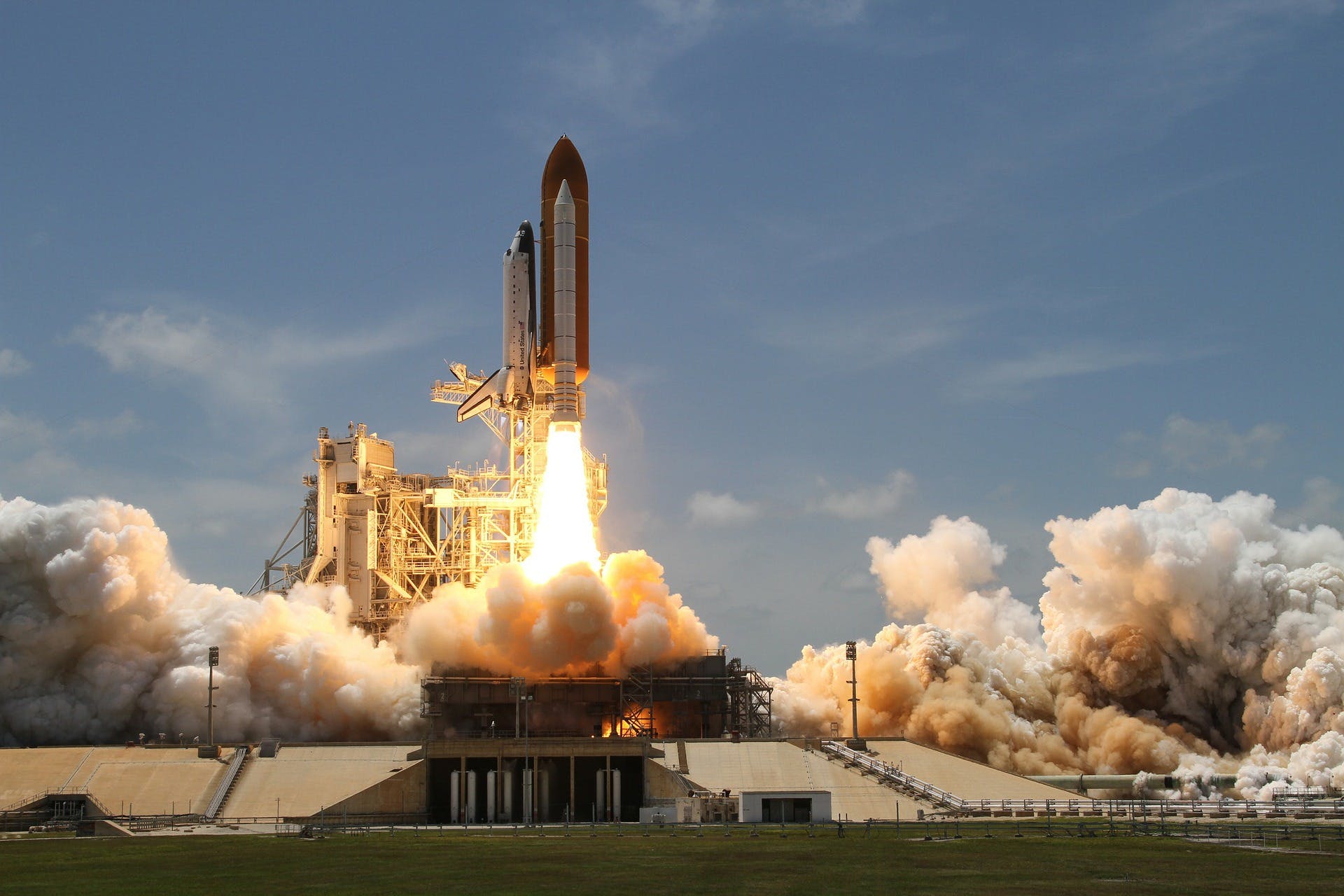
Hydrogen atmospheres have multiple benefits when it comes to heat treating steel components. The atmosphere allows for the material’s strength and magnetic properties to be balanced out. One way this is done is through the reduction of oxidation during the initial annealing process. Oxidation reduces the strength of the component, which is not what you want to happen at this stage. Surface-level oxidation can be beneficial, but not if it intrudes further into the part.
The other reason to use a hydrogen atmosphere is to remove residual carbon from within the steel. This process is known as decarburization and is when the carbon near the surface of the part reacts with the hydrogen in the atmosphere, thus being removed from the part. Decarburization softens the metal which will make it easier to work with. A hardening treatment, such as tempering, is often done after the part is finished being worked to harden it once again.
Oxidizing Finishing Layer
After the annealing phase is complete, an oxidizing finishing layer can be beneficial for improving durability and resistance to wear. The hydrogen atmosphere is removed from the furnace and replaced with an oxygen atmosphere to perform the oxidizing operation. This comes at the cost of some strength, which is why it is important to closely monitor this stage of the heat treatment process.
Batch Processing
If heat treating products with varying shapes, sizes, materials, and more is central to your business, you need a reliable batch processing furnace. L&L’s XLC246 is a batch furnace that can perform both annealing and oxidizing, with the ability to introduce hydrogen and oxygen atmospheres separately. Our XLC series furnaces, along with every other L&L furnace, are also NFPA compliant.
L&L Special Furnace
Many components used within the aerospace industry require specialized heat treatment to be able to withstand the stresses and wear they undergo during normal use. Annealing and oxidation are two of the most common heat treatments for such parts, and L&L has the perfect line of furnaces for the job. Contact us today for more information about our XLC series or other furnaces.