Carbonitriding is a process by which carbon and nitrogen are introduced to the surface of a steel part. The goal of this process is to form an austenite (above A3) which becomes a martensite matrix microstructure after quenching. If there is too much nitrogen introduced to the steel, it can result in retained austenite, which is austenite that does not become a martensite microstructure after quenching. This can cause problems such as increased porosity, by which many small holes weaken the structure of the material. For this reason, it is extremely important to use the proper heat treatment atmosphere, quenching medium, and overall carbonitriding process.
Carbonitriding Process
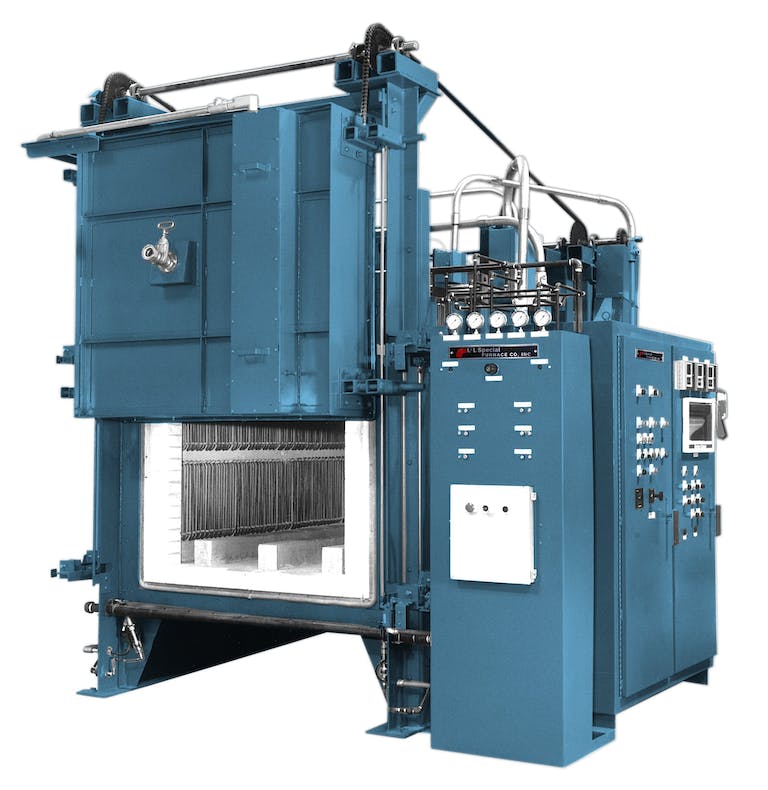
Atmosphere: The carbonitriding process is similar to the gas carburizing process, but with the addition of ammonia alongside the carbon. This process adds 0.5 – 0.8% carbon and 0.2 – 0.4% nitrogen to the surface of the steel. The nitrogen comes from the ammonia present in the atmosphere.
Heat Treatment: The temperature used for carbonitriding should be around 850°C (1550°F). This is lower than the temperature used for carburizing, and the time for which the part will be heat treated for is shorter as well. These lower temperatures used for carbonitriding compared to carburation also means there is less distortion of the part, especially during quenching. However, this is a higher temperature than what is used for standard nitriding.
Quenching: Once the part has been heat treated, it should be immediately quenched in either oil or gas with a protective atmosphere. While water is another possible quenching medium, mild steels can distort more when quenched in water. For this reason, quenching in oil or gas with a protective atmosphere is recommended over water.
Case Hardening Depth (CHD): The case hardening depth is how deep into the surface of the steel the hardening process permeates. This depth depends on a variety of factors, including the carbonitriding depth, hardening temperature, quench rate, hardenability of the steel, and the dimensions of the component.
Benefits of Carbonitriding
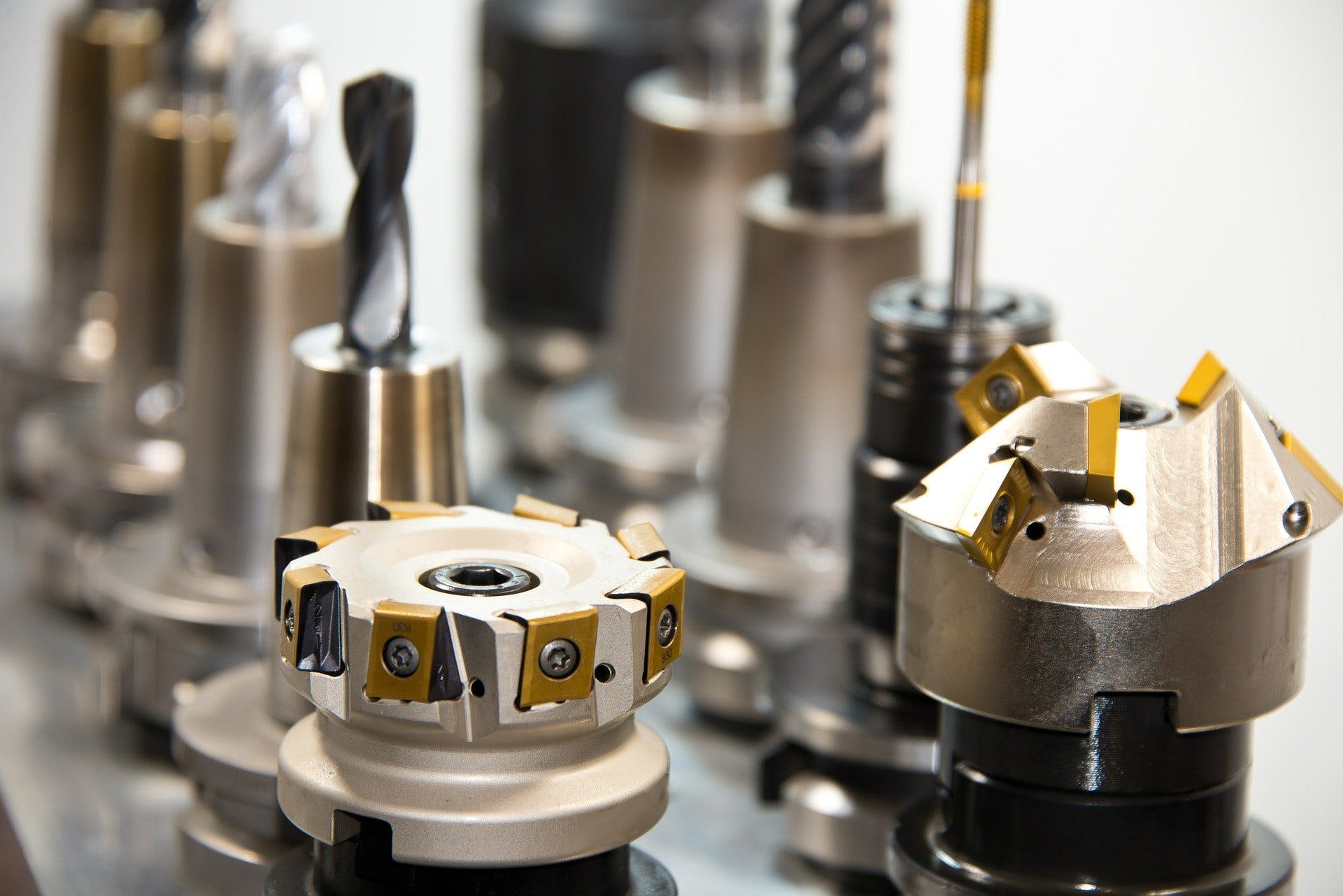
As previously mentioned, the goal of carbonitriding is to give the steel a harder outer shell. However, the hardened case is not an additional layer on top of the steel. The carbonitriding process alters the top layer of the component so the original dimensions are retained. This case hardening is typically between 0.07 – 0.75mm thick. A thicker case means more wear protection, but anything beyond 0.75mm won’t usually be worth the time and effort it takes to achieve. Additionally, the hardness of the shell can increase up to 65 – 66 HRC on the Rockwell scale which puts it in the “very hard steel” category.
The martensite matrix microstructure which results from carbonitriding is one of the primary benefits of using this process. This microstructure is what gives the outer layer of the steel its increased durability, wear resistance, and ductility. Due to this increased durability and wear resistance, carbonitrided parts have increased lifespans in poorly lubricated and contaminated environments which would normally be too extreme for their untreated counterparts. Additionally, parts treated in this way have compressive residual stresses of -25ksi (-172MPa).
Other benefits of carbonitriding include the fact that it’s perfect for the mass production of small components. The smaller the component, the easier it is to achieve a higher case depth. There’s also the resistance to softening during tempering, and an increase in impact strength which can be valuable properties in certain situations. And, both carbonitriding and carburizing can be done together to combine their properties.
Carbonitrided Part Applications
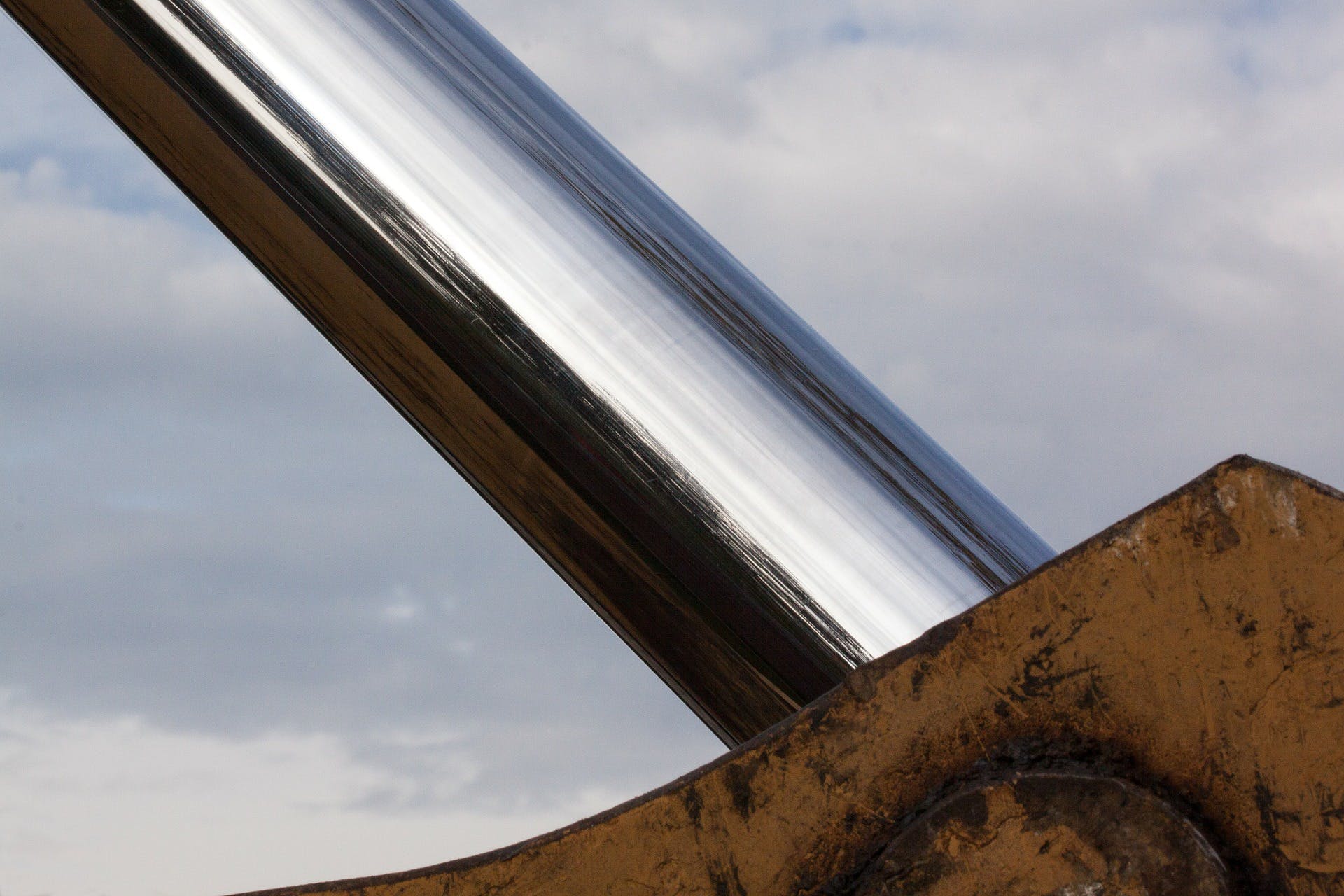
When it comes to the types of steel which can be carbonitrided, there is a wide variety which includes plain carbon, mild (reduced aluminum), low alloy (0.25% carbon maximum), free cutting, and sintered steel. The steel used is going to depend on what the component is eventually going to be used for. Some of the most common parts which rely on carbonitriding are gear teeth, cams and shafts, bearings, fasteners and pins, hydraulic piston rods, automotive clutch plates, tools, and dies.
Looking at just a few of these possible applications for carbonitrided steel, we can see exactly how the benefits of this process work in the real world. For example, hydraulic piston rods can benefit from the increased lifespan carbonitriding provides in poorly lubricated and contaminated environments. Poor lubrication within a hydraulic cylinder can cause metal flakes to be sheared off and contaminate the system. This contamination then leads to an increase in wear, eventually destroying the cylinder from the inside. Some hydraulic cylinders are sealed for life, meaning their lubricant cannot be changed out when it becomes contaminated. Situations like this are why carbonitriding is so important to prevent wear.
Conclusion
Carbonitriding is a heat treatment process by which carbon and nitrogen (via ammonia gas) permeate the surface layer of steel components. The process involves temperatures of around 850°C followed by quenching in oil or gas solutions. Successful completion of this process will grant the steel components a variety of beneficial properties, most notably increased wear resistance. And there are many different applications for carbonitrided parts in high-wear situations such as gear teeth, bearings, and tools.
L&L Special Furnace
L&L Special Furnace manufactures industrial heat treatment furnaces for a wide variety of applications, including carbonitriding. Contact us today for more information on our furnace specifications and help selecting which furnace is right for your particular need.