
Injection molding is one of the primary ways to manufacture parts out of powder metal. The main benefit of using injection molding is that it can produce parts that are complex in nature. However, it is generally reserved for manufacturing small parts that weigh less than 100 grams. The injection molding process has four main steps. First, the powder metal and a binding agent are mixed into a feedstock. Second, the feedstock is injected into a mold of the part. Third, the binding agent is removed from the “green” part. And fourth, the part is hardened by sintering. This relatively simple process is what makes injection molding such a cost-effective means for producing small parts.
Mixing Powder Metal and Binder into Feedstock
The feedstock is made out of two components. Spherical, metal powder that is less than 25 microns in size is the primary component and what the final part will be made of. Plastic or wax is the second component and is used as a binding agent, also known as the binder. The binder is only a temporary component and will not be present in the final product after heat treatment is completed. To create the feedstock, the binder should first be heated until molten. Then, the metal powder is mixed in until the grains are entirely coated by the binder. The resultant mixture should be 60% powder and 40% binder by volume.
Injection Molding the Feedstock
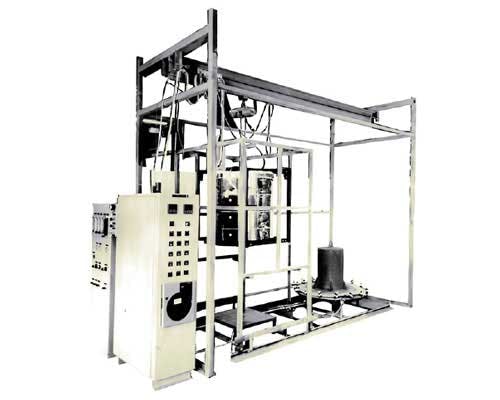
Once the feedstock is created, it is heated and injected into a mold of the part under high pressure. The mold cavity that the feedstock is injected into will be about 15 – 20% larger than the final product. The exact size of the mold compared to the final part dimensions will need to be calculated based on the materials used. During the final phase of the manufacturing process, the part will shrink down to the correct size.
The molding process is done at about 392℉ (200℃). This is because greater compression of the part is allowed if the binder is molten. Without a molten binder, the porosity of the metal powder cannot be completely removed and will result in a part that is far more porous than intended. The end goal of powder metal injection molding is to create a part with nearly 0% porosity. A special injection molding machine is necessary for this step of the manufacturing process.
Debinding “Green” Injection Molded Parts
After a part has been injection molded, it is referred to as “green.” This green part still contains most of the binder that was used during the molding process. Before moving onto sintering, which is the final step in the manufacturing process, the binder must be removed from the part. This can be done in multiple ways. But the most common is through solvent extraction, in which the part is submerged within a solvent that breaks down the binder. The majority of the binder can be removed in this way, and what little remains will evaporate out of the pores during sintering. With the binder removed and the part ready to be sintered, it is now in the “brown” stage.
Sintering “Brown” Powder Metal Parts
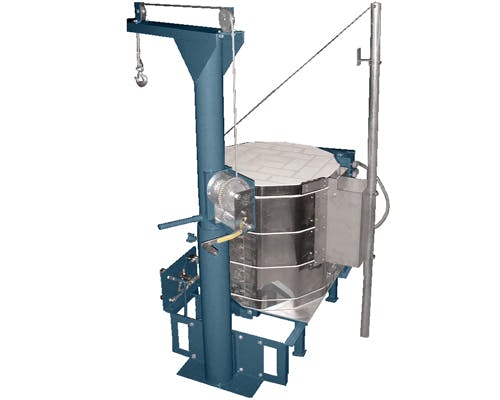
Brown parts are very fragile. Although they resemble the final product in shape (but are about 15% larger), the powdered metal that makes them up has not yet been hardened into place. The only thing holding the powder together at this point is the very small amount of binder remaining.
The sintering process begins with the brown parts being loaded into a sintering furnace with a controlled atmosphere. Initially, they are heated at a lower temperature to remove the remaining binder. They are then heated at a high temperature near the melting point of the metal being used. This causes the metal powder particles to fuse, eliminating the remaining porosity left over by the removal of the binder. During this phase, the parts will shrink by the aforementioned 15 – 20%. This shrinking of the part and fusing of the metal particles causes the final product to be very dense.
After sintering is complete, the final product can additionally undergo further heat treatment processes if necessary. Platings or coatings can also be applied. And the parts can even be welded or cold worked without the risk of damage.
Conclusion
Powder metal injection molding is a popular and cost-effective manufacturing process for small, complex, highly-dense parts. The process begins with powder metal and a binding agent being mixed into a feedstock at a ratio of 60:40. The feedstock is then injected into a mold of the part that is about 15% larger than the final product will be. After the molding is complete, the binder is extracted from the newly green part via solvents. And lastly, the part is sintered, removing the remaining binder, shrinking the part down to its final size, and hardening it.
L&L Special Furnace
At L&L Special Furnace, we manufacture a wide variety of furnaces for industrial uses, including specialized sintering furnaces. If you are in need of an industrial furnace, contact us today. Furnaces that can be used for powder metals include the XLC, JSC, and JDR series.