Brazing copper in a hydrogen atmosphere is used for the creation of strong joints that can withstand high pressures and temperatures. Copper can be brazed to itself or other materials without the need for a brazing flux when hydrogen is used as the atmosphere. For this reason, the copper and hydrogen combination is one of the most versatile when it comes to brazing.
Copper Brazing Process
Copper brazing in a hydrogen atmosphere has three main parts: the atmosphere, the filler metal, and the cooling process. The atmosphere includes the gas, pressure, and temperature. The filler metal used depends on the material the copper is being brazed to. And the cooling process is purposefully slow to prevent damage to the brazed part.
Atmosphere
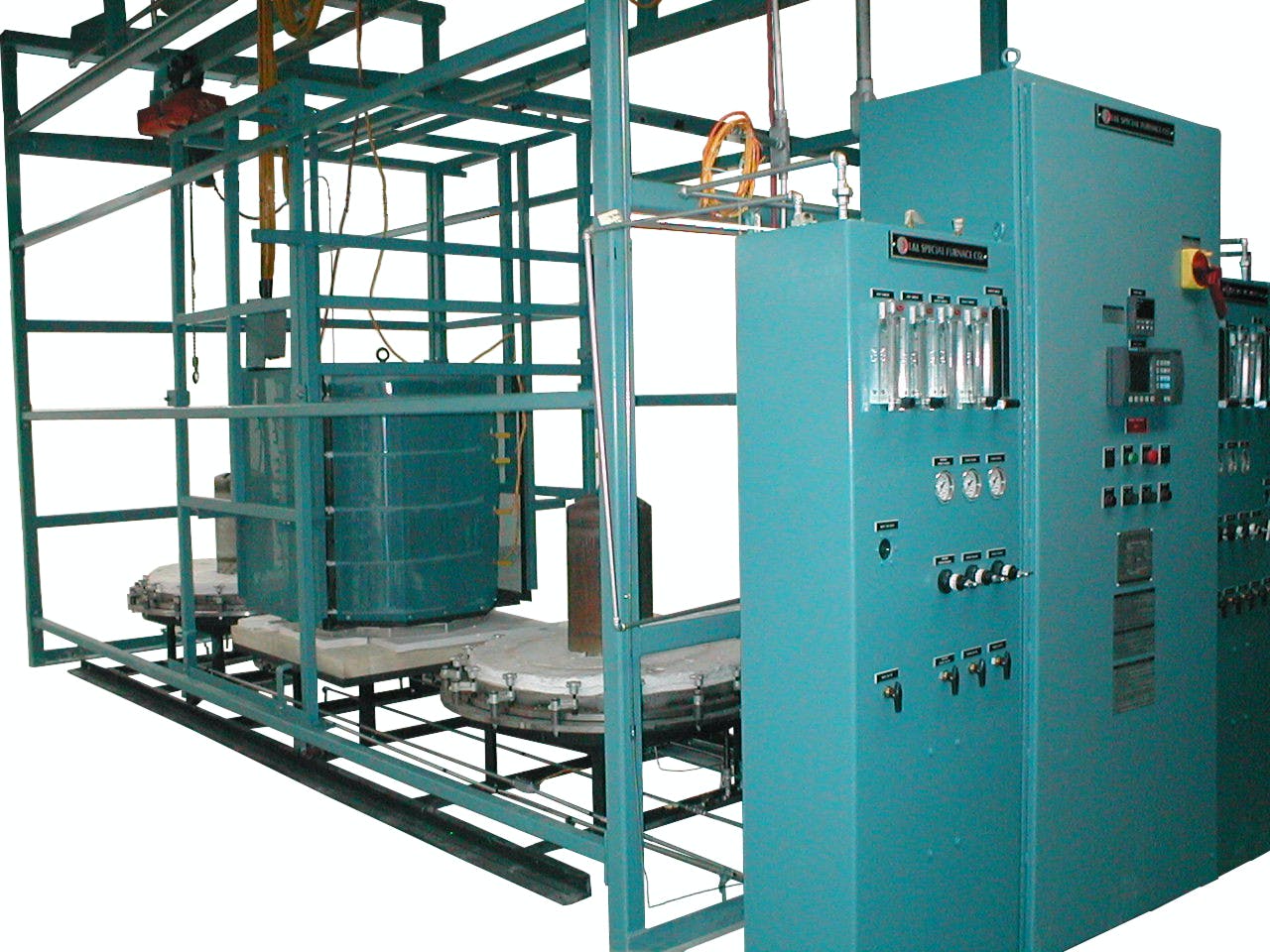
The H2 gas atmosphere is the most important part of the setup for brazing copper because the hydrogen acts as a brazing flux. Brazing fluxes for copper are usually water-based solutions that protect the surface of the part against oxidation and remove residual oxides from the part. However, H2 gas functions in the same way and so streamlines the process because an additional flux is not needed.
Copper is typically brazed in “wet” hydrogen as opposed to “dry” hydrogen. Wet hydrogen is used when removing residual hydrocarbons is preferred, while dry hydrogen is the superior choice when the removal of additional oxides from the material is most important. For copper, wet hydrogen is better in most situations. The only time you should consider dry hydrogen is when the copper is being brazed to a material such as stainless steels that are high in oxides.
The atmosphere within the furnace should be slightly positive when brazing with hydrogen, and the temperature will depend on the metal being brazed. For copper, the optimal temperature will usually be between 1,100 and 1,500℉. The temperature is also important for the next part of the brazing process, the filler metal.
Filler Metals
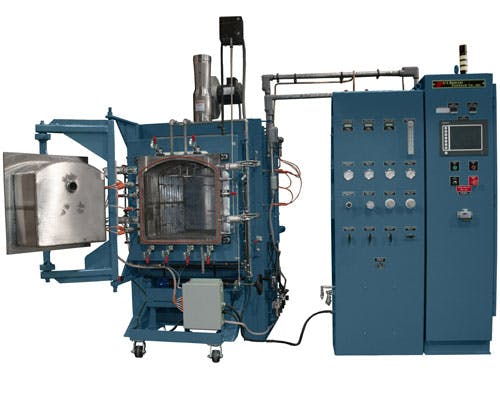
In brazing, the materials being joined are not melted together to create a joint. Instead, a filler metal is melted onto the connection point and cools to create a stronger joint than would otherwise be possible. The key to picking a filler metal is to pick one that has a lower melting point than the materials it is being used to join together. For example, copper has a melting point of 1,949℉, so the filler metal would need to have a melting point below that if it was being used to join two copper parts. Additionally, the melting point of your filler metal will set the lower bound for the temperature within the furnace. While the furnace temperature should not be above the melting point of your main materials, it should also not be below the melting point of your filler metal.
Cooling
Copper parts should be naturally cooled in air after brazing is complete. Unlike many heat treatment processes, brazing does not make use of rapid quenching in liquid media as this can cause the part to become brittle and crack. After cooling is complete, if a brazing flux is used, the flux residue will need to be wiped off the part. This is an additional benefit to using H2 gas because this step can be skipped as there is no residual flux to remove.
Should You Braze in a Hydrogen Atmosphere?
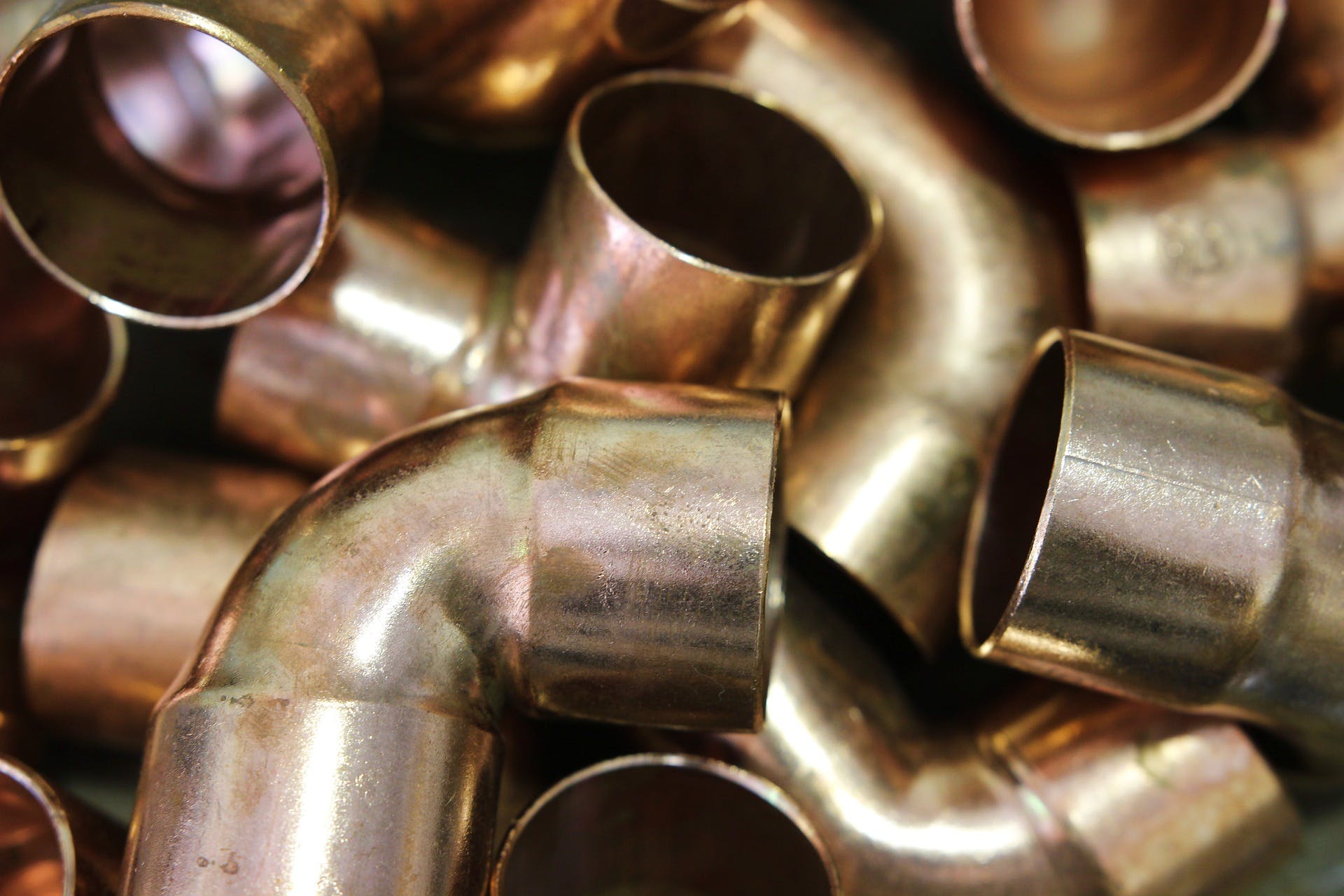
When considering whether or not to braze in a hydrogen atmosphere, there are a few questions you should ask yourself. First, is brazing the right process for what you are trying to achieve? The primary benefit of brazing is that it does not melt the base metals the individual parts are made of. This means that the parts are not weakened in order to be joined together. Instead, the filler metal does the job of solidifying the connection point. If you require strong joints, brazing may be the right option.
The second question you should ask is whether or not a hydrogen atmosphere is your best choice. If you are brazing copper, then you will want to stick with hydrogen for the vast majority of situations because of its two primary benefits we have already touched on: It does not require an additional brazing flux and it is able to either remove residual hydrocarbons or reduce oxides depending on whether the hydrogen is wet or dry.
Safety is another aspect of brazing in a hydrogen atmosphere that you should keep in mind. Hydrogen is a flammable and explosive gas, so heating it in a furnace can present hazards. Furnaces that are designed to be used with hydrogen atmospheres come equipped with a few safety features. Oxygen levels are monitored and excess gas is burnt off to prevent it from building up within the furnace. At L&L Special Furnace, manufacture two furnaces that are rated for brazing in hydrogen atmospheres: the JSC and XLC series.
Conclusion
When strong joints are needed, such as in copper piping that must withstand high internal pressures, brazing is the optimal process for the job. It makes use of filler metals to form the connection between two parts so the parts themselves do not need to be melted and suffer from a reduction in strength. Additionally, using a hydrogen atmosphere has its own set of benefits when copper is the primary material being brazed. It removes the need for a brazing flux and also serves to remove unwanted substances from the parts. Finally, when the brazing process is complete, the combined part should be left to cool in air — no rapid quenching required.
L&L Special Furnace
At L&L Special Furnace, we manufacture high-quality, industrial furnaces for a variety of industries and heat treatment processes, including the brazing of copper parts in hydrogen atmospheres. Contact us today to learn more about our JSC and XLC furnaces for brazing processes, or any of our other heat treatment ovens and furnaces.