The process we know as additive manufacturing (AM) may seem new, but it has actually been around for about thirty years. This has given it plenty of time to mature into an effective manufacturing process for everything from customized prosthetics to jet fuel nozzles. Parts made using AM can be found in everything from unmanned ground vehicle hardware to complex investment casting patterns. AM is ideal for making parts that have extremely complex geometries, require extreme heat resistance, and may involve significant customization.
Additive Manufacturing
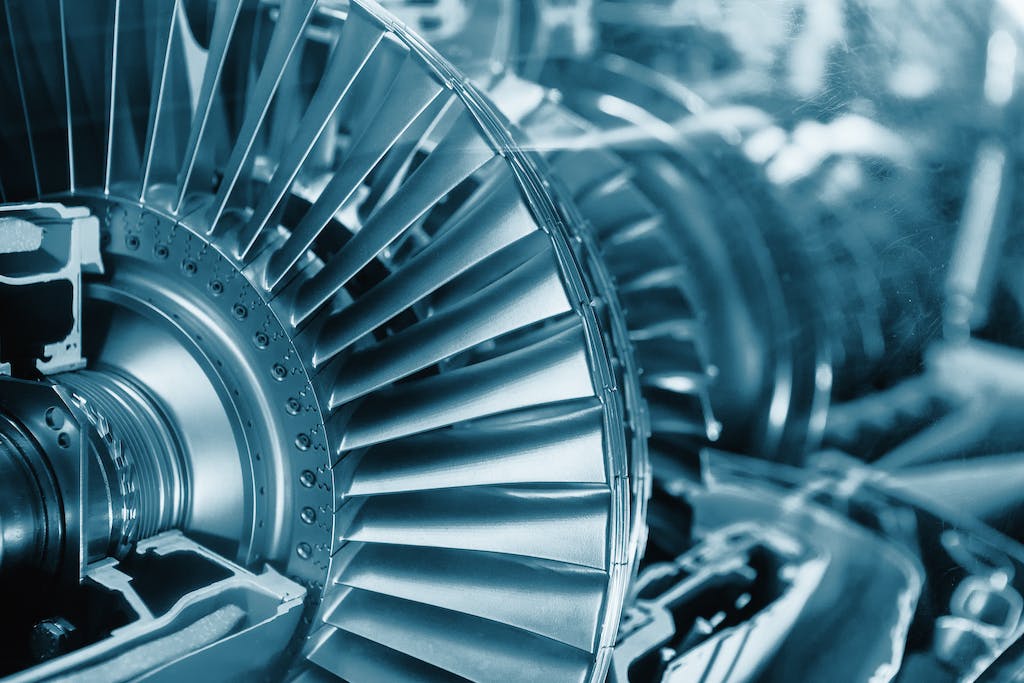
According to ASTM F2792-21a, AM refers to the process of making an object from 3D data by joining materials, typically a thin layer at a time, as opposed to subtractive methods such as milling or turning that remove material in order to form the final object. Other terms for this type of process include additive layer manufacturing, additive fabrication, additive techniques, layer manufacturing, and freeform fabrication. Terms such as 3D printing, direct digital manufacturing, and rapid prototyping actually represent subsets of AM.
Overview of Additive Manufacturing
In AM, superfine layers are created one at a time, building up to the final shape. That final shape is based on a 3D model, which could have been scanned from an existing object or generated using CAM software. The 3D model is then transformed into the individual layers that will make up the final part, which is then used by the computer-controlled AM equipment to manufacture the part. After the layers are either cured or cooled, the final part is ready.
What Makes AM Different
As mentioned, AM is the opposite of subtractive manufacturing. In subtractive manufacturing, material that is not needed in the final part is removed. This is not the case with AM, which only uses as much material as is necessary and thus makes efficient use of materials. Another aspect that makes AM so different from more traditional methods involves how changes to the geometry can be made just minutes before the part is made with minimal impact on the production. This is not the case with methods involving metal forming, dies, or casting. It is economical for short production runs, which means AM works extremely well for parts intended for retrofitting or highly-customized designs.
There is another facet of AM that makes it different from more traditional methods: it uses far less energy and materials to make components. This simple fact means that AM is actually a green alternative to manufacturing – something the vast majority of manufacturing processes cannot lay claim to.
Computer-Aided Manufacturing
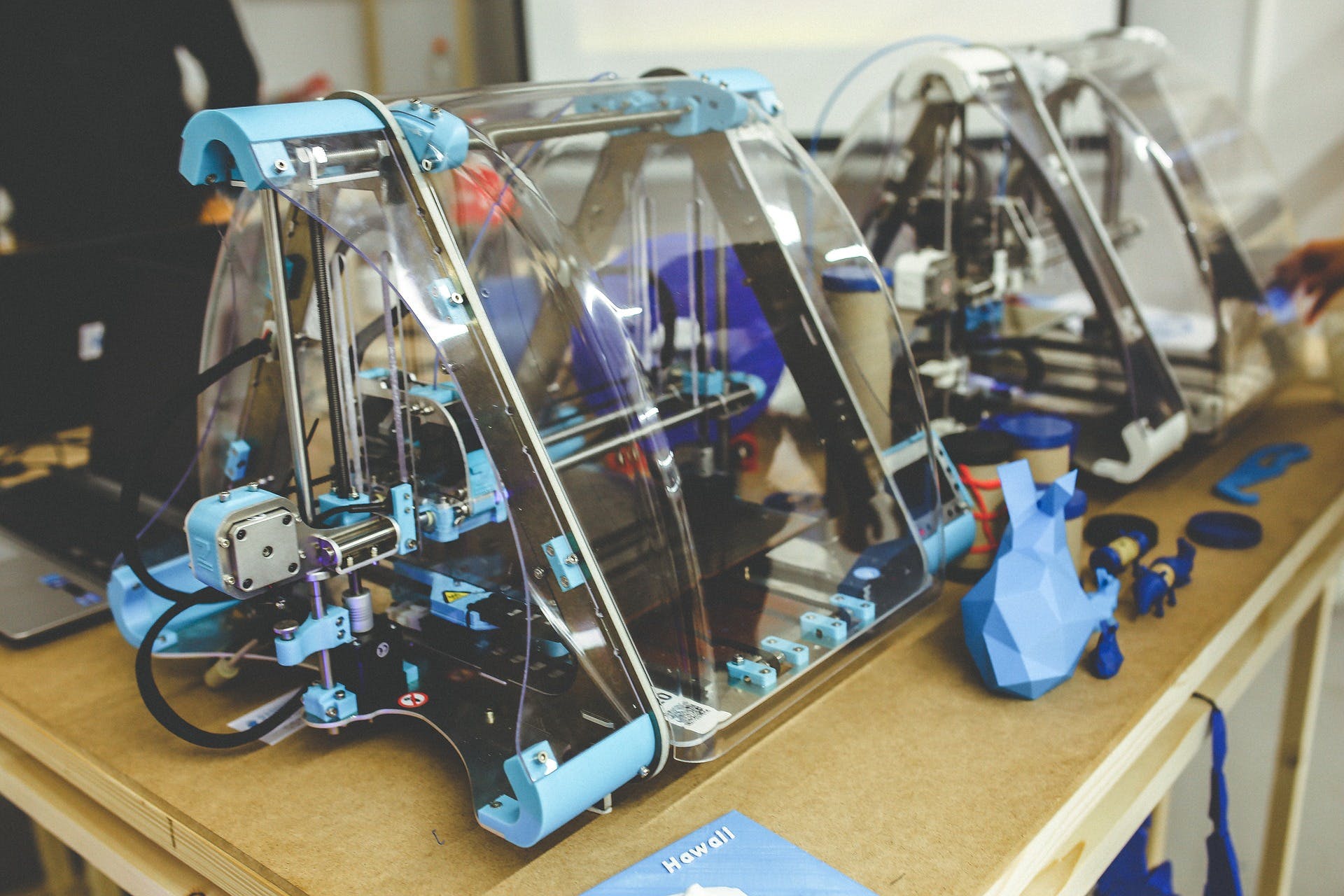
Another important aspect of additive manufacturing involves the intrinsic use of computers all the way from design through manufacturing. As alluded to earlier, a 3D model of the desired part is generated using a computer along with CAD/CAM and other solid modeling software. Once the 3D model is complete, the model is sliced into extremely thin layers which become the layers built up during the AM process. In addition to the layers, software will determine where supports are needed, and those supports will also be transformed into layers.
The layered model is transformed into a sequence of commands very similar to the M&G code used in CNC machining. Those codes are used to move and activate the laser (in the case of laser sintering) or the nozzle (in the case of 3D printing) with great precision. In some cases of 3D printing, it may be the print bed that moves instead of the nozzle.
Materials for Additive Manufacturing
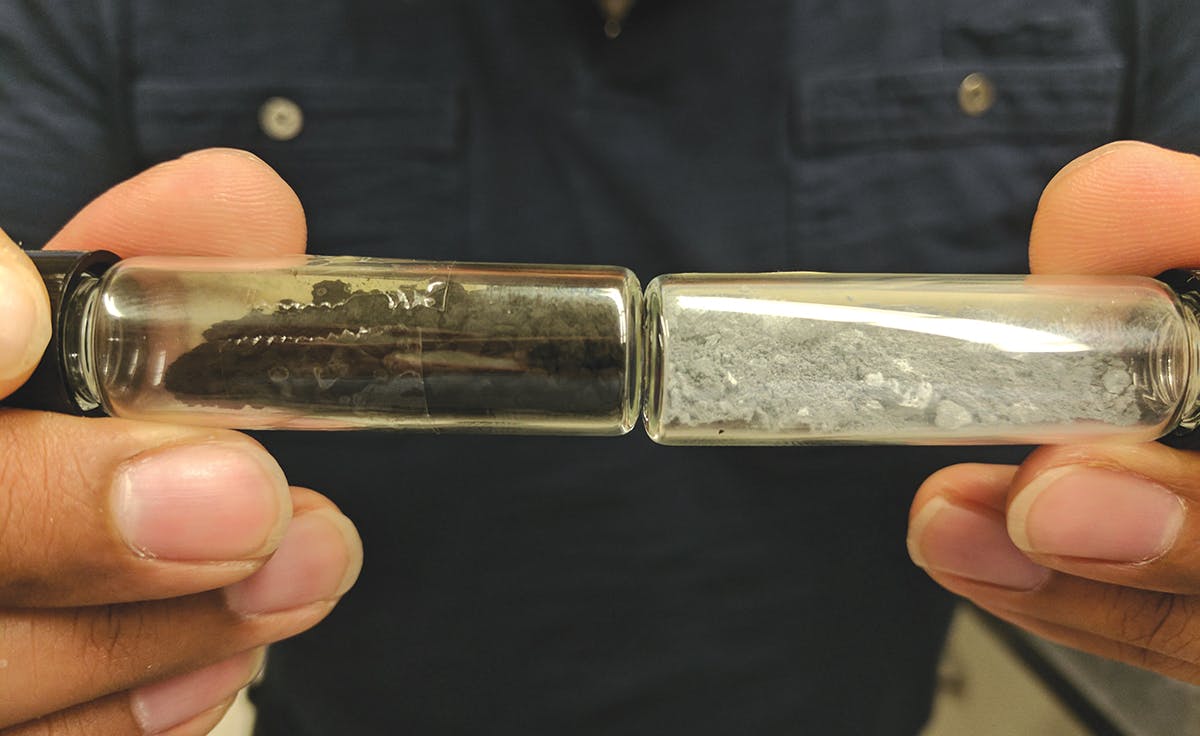
There are so many different types of materials that modern AM supports, including ceramics, metal powders, thermoplastics, foams, gels, biomaterials, and composites materials. Ceramics such as tricalcium phosphate, zirconia, and alumina are often used in AM, as well as glass. While precious metals may be used, most of the time you will find metal alloys of aluminum, stainless steel, and titanium used in AM. Biomaterial examples include calcium phosphate and zinc to support bone growth for parts intended for use inside the human body. Bio-inks that make use of stem cells are also being developed. In some applications of 3D printing for architecture and construction, materials such as cement, concrete, or stone-like powders are being used.
In addition, AM can generate parts with functionally graded materials. For example, a part may need a titanium or stainless steel interior for strength but a ceramic exterior for high resistance and abrasion resistance. AM supports this approach.
Sintering of Additive Manufacturing Components
Sintering is a key step in the process of AM, and it refers to fusing particles together to form the final part. The fusion process itself may involve melting, depending on the material being sintered and sintering may be integral to the actual layering process. Components manufactured using sintering processes are known for their high strength and their heat resistant properties.
Sintering processes can be differentiated by the energy source used, such as selective laser melting versus electron beam melting. There are also different processes used for different materials. Polymers may be additively manufactured by a few different methods, including selecting laser sintering (in which the polymers are softened and fused but not fully melted) and stereolithography (which uses a special type of polymer that hardens based on the type of light it is exposed to). Fused deposition modeling works with both polymers and metals using nozzle extrusion to form the individual layers.
Laser Sintering Process
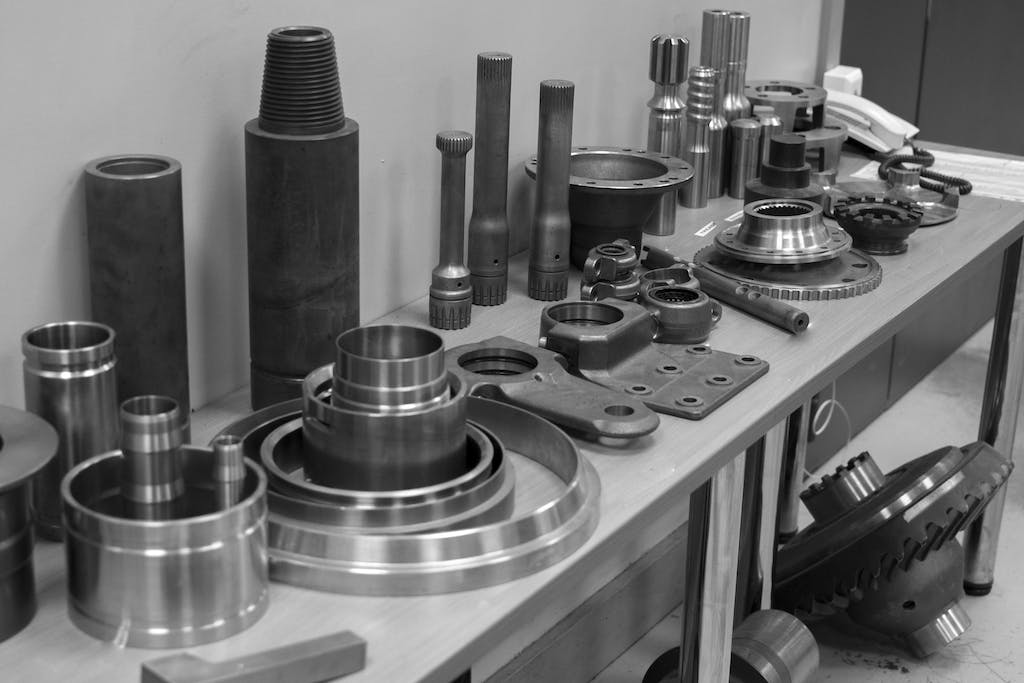
Laser sintering is a commonly used sintering process, and direct laser sintering (also known as selective laser sintering or selective laser melting) is one particular laser sintering process. In this type of sintering process, a directed energy beam in the form of a laser moves across a bed covered with a thin layer of metallic powder. The laser microwelds the cross-section a single layer at a time. Once a layer is microwelded, the build platform moves down and a recoater blade is used to distribute another layer of powder. The build continues, layer by layer, in an inert atmosphere.
Direct laser sintering makes it possible to build a functional prototype or part that is almost 100% dense which is manufactured within a very short amount of time. Essentially, this type of process amounts to the 3-dimensional printing of metal parts made from materials such as cobalt, chrome, Inconel, titanium, aluminum, and stainless steel.
Post-Sintering
After sintering is complete, any loose powder is removed and the part is then subject to material and application-specific heat treatment processes. Note that the part may remain in its printed support structure during heat treatment. Typical heat treatment processes include the following:
- Sinter hardening for increased surface hardness (requires a carbon-controlled atmosphere)
- Tempering (e.g., martempering, austenitizing) for increased toughness
- Stress-relieving
- Hot-Isostatic Pressing (HIP) to achieve maximum density, heal defects, and close pores
These processes are key to the quality and final properties of the part as they increase the density, refine the microstructure, and harden the surface.
Most of these processes must take place in a heat treatment furnace that provides very precise, regulated temperature and a highly consistent inert atmosphere of nitrogen, argon, or hydrogen, or even a vacuum. During heat treatment, sintered parts can be contaminated by exposure to oxygen. In such situations, oxygen contamination will reduce the porosity of the final part, which in turn compromises key physical and chemical properties. Finally, it is important to keep in mind that some heat treatment processes for AM parts may require subsequent quenching.
Additive Manufacturing Applications
Many people associate AM with the development of prototype parts as was the case in its early days. In reality, many components manufactured using this method currently are intended for real-world applications. These applications often involve exposure to less than ideal operating conditions, including caustic chemicals, biochemical issues, and extreme heat. Because AM supports geometric customization without the costs associated with molds and dies, it has proven ideal for highly customized parts. In fact, many different industries use additive manufacturing to produce usable parts and components.
Aerospace
Aerospace demands lightweight, high-performance parts that often have extremely complex geometries. AM is able to produce such parts with amazing precision, including rocket injectors, fuel nozzles, structural parts, and more. One of the reasons AM is popular in this industry lies in the production volume of parts: unlike automobiles, the production run for aircraft parts is far more limited. Because of this, it can be prohibitively expensive to make molds for complex, highly detailed parts; AM offers a more economical alternative that produces the same (if not better) quality parts.
Healthcare
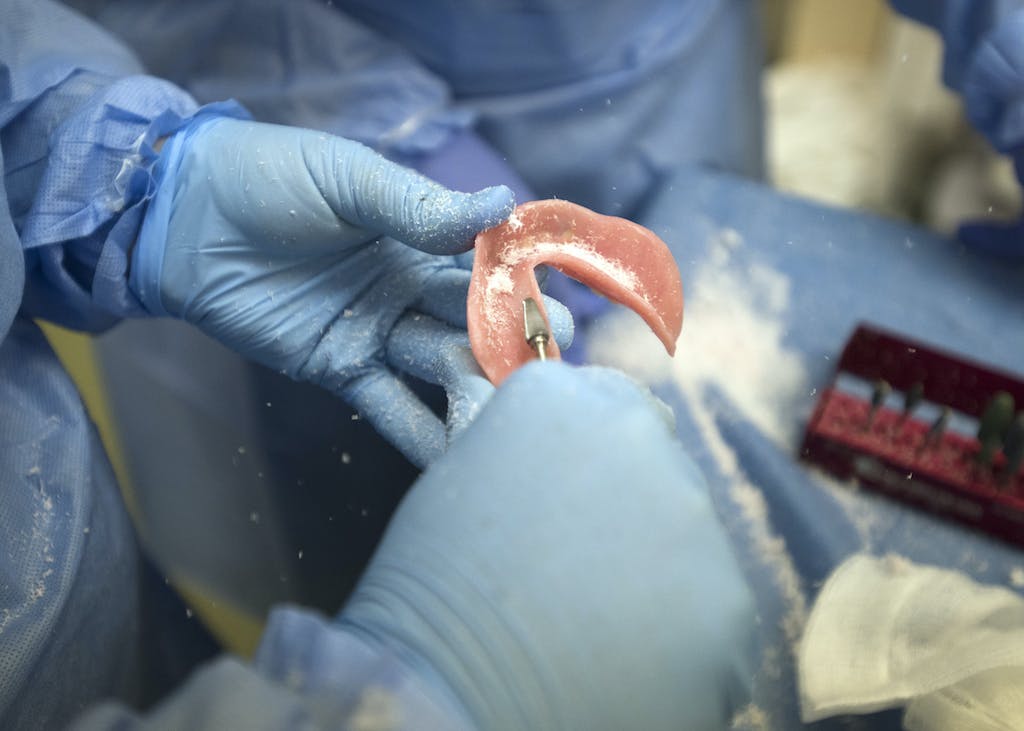
The ease with which additive manufactured parts can be customized is one of the major selling points for this process in healthcare. This has, in turn, led to continuing research into AM applications in healthcare, such as customized surgical implants, dental work, patient educational models, and prosthetic limbs. There is even research being performed into the feasibility of 3D printing human organs, including human skin created from stem cells.
Oil and Gas
The oil and gas industry uses AM for parts such as pump manifolds, mud motor models, down-hole tool components, rotors, turbine nozzles, and stators. You also see fluid and water flow analysis components, flow meter parts, control-valve components, and pressure gauge pieces that have been made via AM.
Automotive
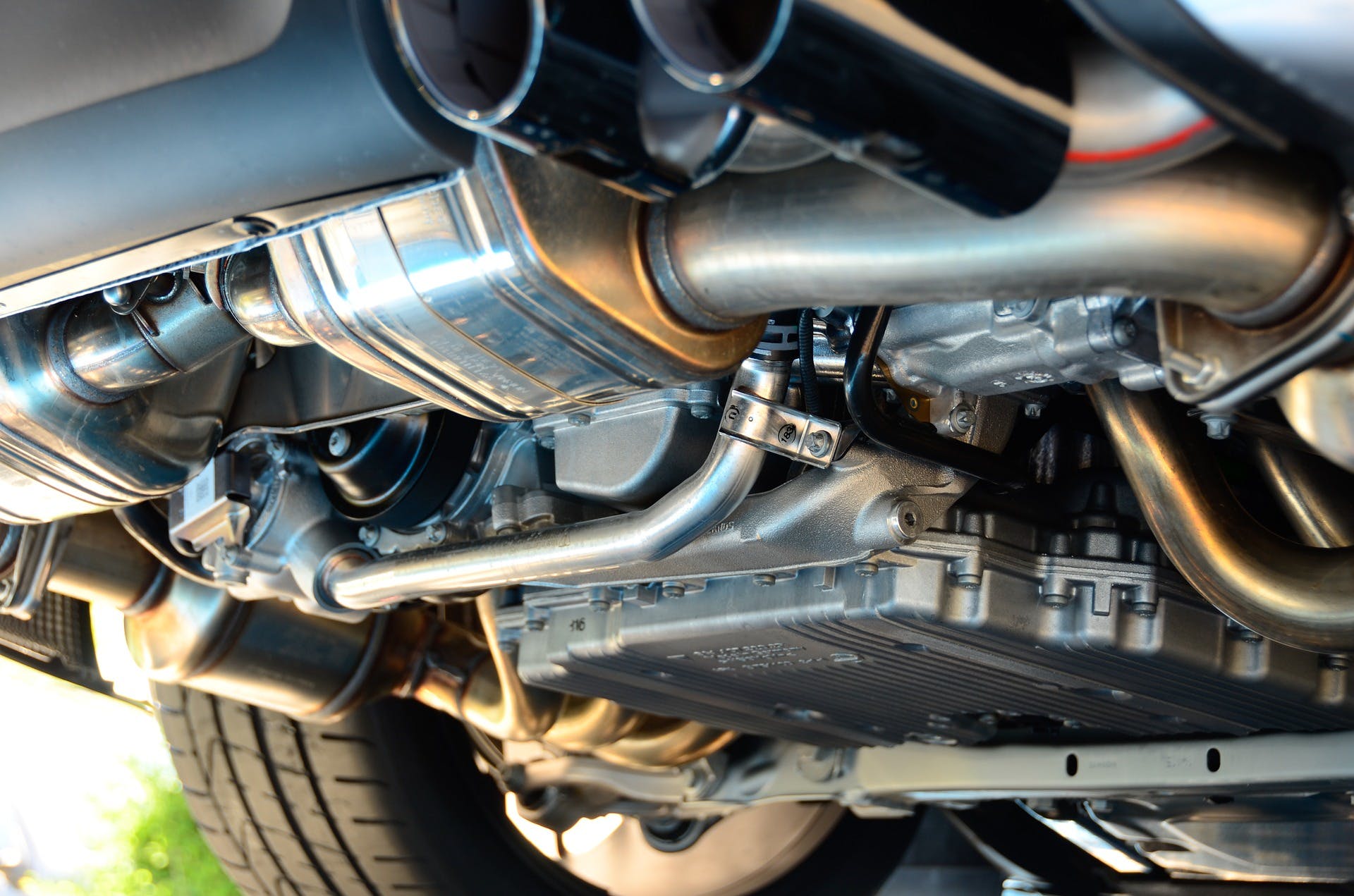
Additive manufactured parts have found their way into Ferrari Formula 1 race cars, including rear wing replacements, as well as production parts for automobiles, including exhaust pipes, bumpers, grilles, complex ductwork, and pump components. Ford Motor Company has implemented AM for the manufacturing of many different parts, both large and small. One of the benefits of AM is the ability to manufacture parts with a thickness that can be optimized to provide the necessary strength and stiffness while remaining lightweight.
Tooling
Additive manufacturing is also being used to make tooling for components in a variety of industries. This can include complex dies and molds that cannot be effectively manufactured using traditional manufacturing methods. Along different lines, AM is being used on the International Space Station to print tools and replacement parts as needed.
Complex Shapes
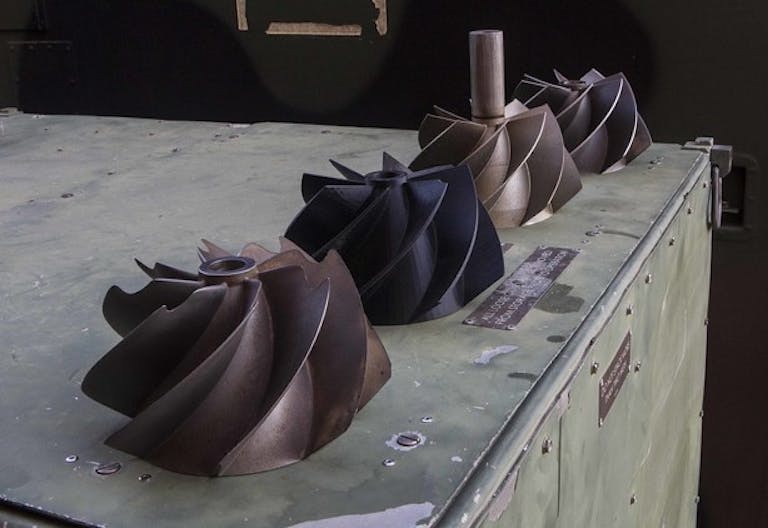
Because of the layer by layer approach taken by AM, parts that would at one time have been impossible to make have been rendered feasible. For example, subtractive manufacturing such as milling can run into problems with tool clearance or access, whereas AM faces no such problem. These parts may not be feasible using molding methods because of features such as undercuts. This also means that there are some parts that simply cannot be manufactured any other way but by AM.
Construction
AM methods are being used to build simple things such as functional footbridges as well as the shell for homes. These large-scale implementations typically use a 3D printing approach with equipment that is taken onsite to print supports, walls, and foundations. The layers are generated using a nozzle system (e.g., material jetting) to distribute the material (e.g., concrete or cement). There are also examples of construction equipment using 3D printed parts, including working compact excavators.
Practical Examples of Additive Manufacturing Using Metals
AM was used with great success in the development of a transplant jaw for an elderly woman in 2012. The jaw was made from titanium powder and a selective laser sintering process was used. The actual printing process only took a few hours, and was followed by heat treatment and the addition of a bioceramic coating.
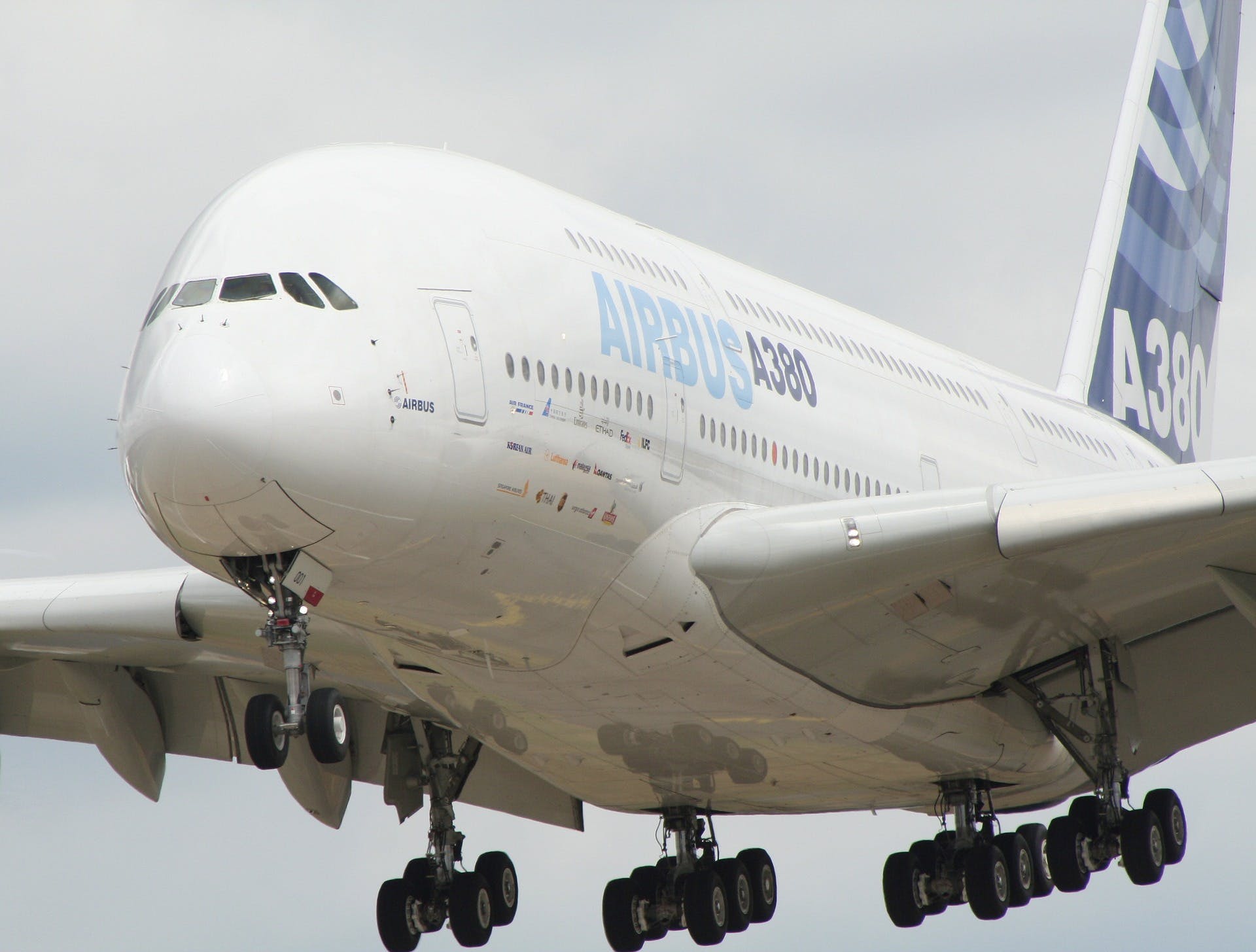
In 2015, the massive Airbus had over 1,000 of its parts produced using AM in order to meet delivery deadlines. However, 2018 marked the first time that passengers would be able to see a retrofit part that was 3D printed: polymer spacer panels. Airbus also uses AM for a variety of metal parts made from aluminum, titanium, and stainless steel, and such parts are now a part of serial manufacturing for several models of aircraft.
GE is a leader when it comes to AM, including its use to speed up the repair of jet engine components. Instead of developing a 3D model of a jet engine part, an existing part is scanned and can then be repaired using AM techniques.
The Swedish car maker Koenigsegg used AM to create various components for a fast, lightweight racing car called the One:1. The large and complex titanium exhaust tip took 3 days to print using laser sintering, which was followed by heat treatments and finishing before it was installed and successfully tested.
Euro-K used AM to develop an additively manufactured micro-burner which works with both liquid and gas fuels without having to change out the burner. The powdered metal used in the laser sintering process was Inconel, which is well known for its strength and the high operating temperatures at which it can function at.
Final Thoughts on Additive Manufacturing and Laser Sintering
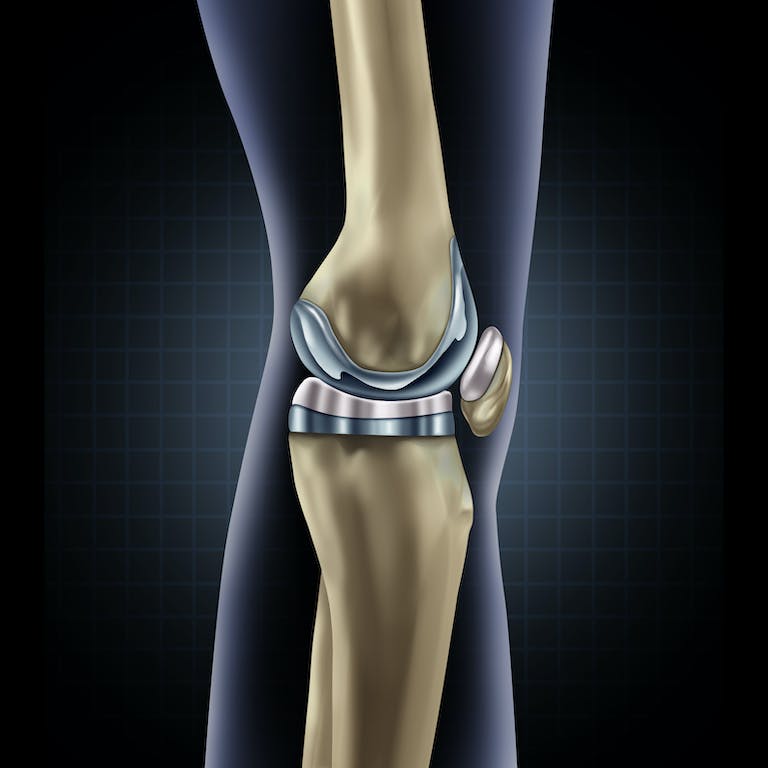
The additive manufacturing process, and the technology supporting it, has matured to the point that it can quickly produce manufactured working components that might not even be feasible (economically or otherwise) using traditional processes. In the past, AM and processes such as 3D printing and SLS were primarily used for rapid prototyping, but now AM supports the generation of highly customizable parts for use in mission-critical applications in industries as diverse as aerospace, medicine, and construction.
When the material of choice is metal, then sintering becomes a major factor in the manufacturing process, followed by heat treatment to achieve improved mechanical properties. In the end, the result can be a highly complex, very strong part that withstands extreme temperatures and aggressive atmospheres, such as those faced by components such as fuel nozzles and automotive exhausts.
L&L Special Furnace Solutions for Additive Manufacturing
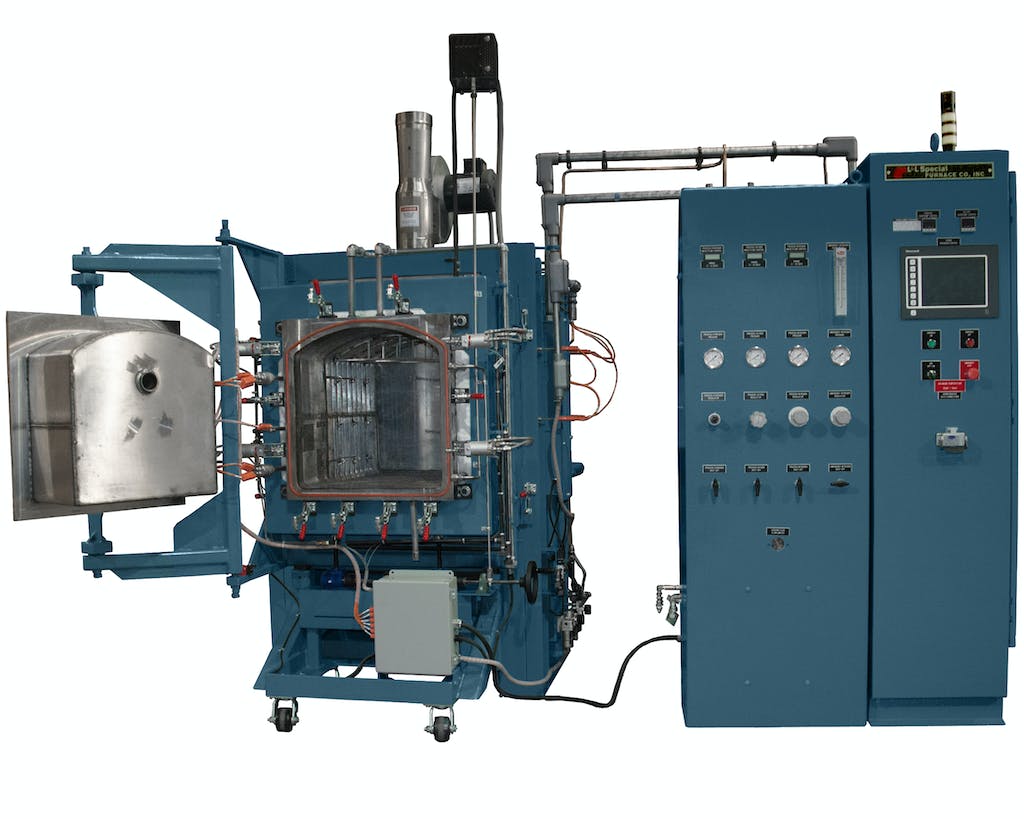
Model XLC244 Retort Furnace with Hydrogen/Nitrogen atmosphere system.
We understand the needs of our customers who work with additive manufacturing, and as a result we offer up-to-date, effective solutions for their heat treatment and industrial furnace demands. We have also worked carefully to align our product offerings so that they are highly customizable and truly able to meet our customers’ heat treatment needs.
When it comes to the heat treatment of AM parts, we have furnaces available that are ideal for such applications. For example, one option is an atmospheric retort furnace like those in our electric-powered XLC series. These retort furnaces provide a highly stable atmosphere and combine the control system, alloy retort, and flow system into a single unified array.
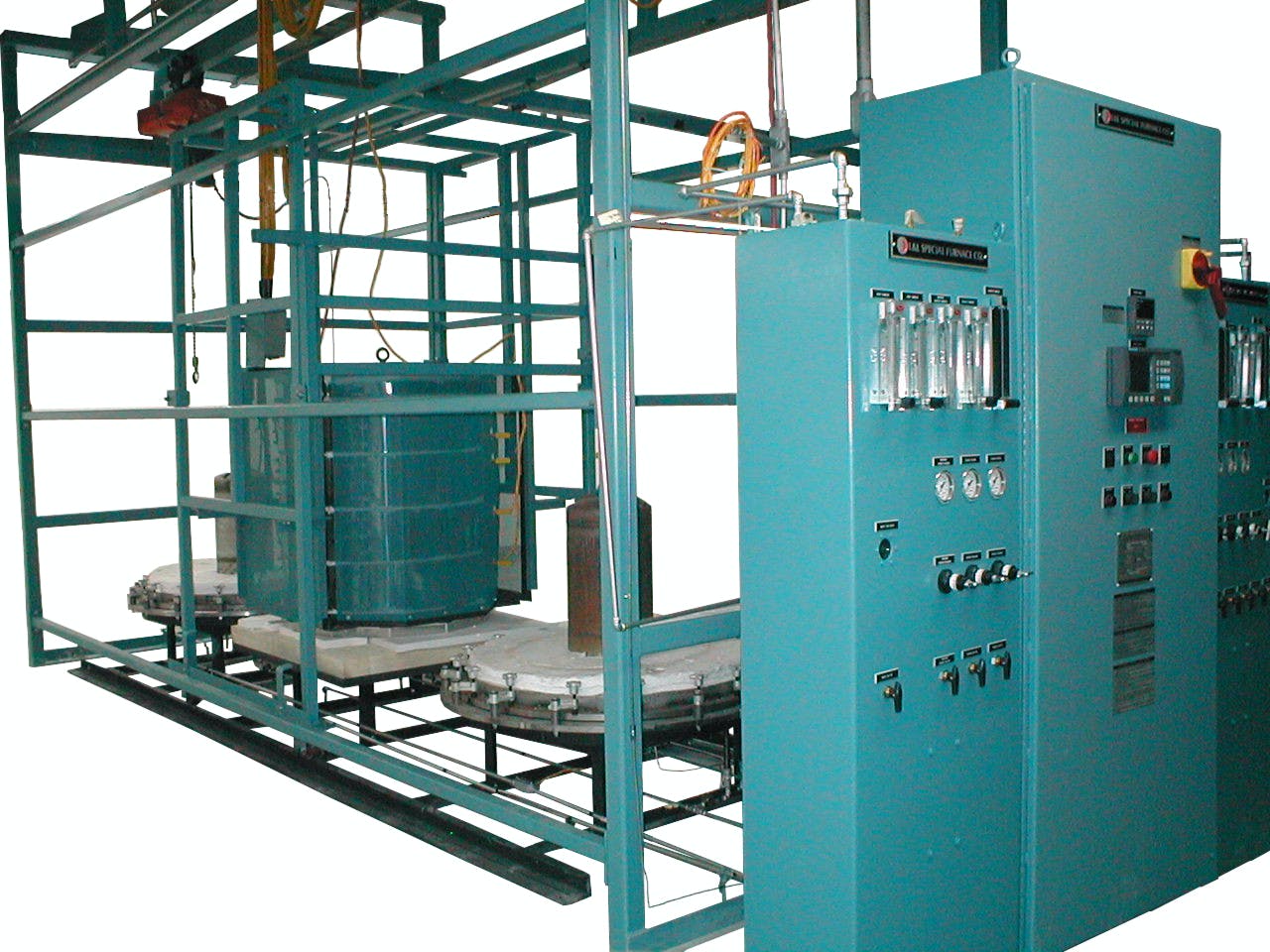
Model JSC1012 Shuttle Retort Furnace with two bases and rest station, equipped with Hydrogen/Nitrogen atmosphere system.
There is also the JSC Series, which is a 2200°F hydrogen atmosphere-controlled shuttle lift retort furnace with a bell-type “top hat” alloy low dew point retort. Any application that requires purely inert atmospheres (including hydrogen or hydrogen mixtures) can be used in the JSC series.
A third option is the GSR1714, which supports an inert atmosphere environment and offers effective and precise multi-program control and even heating. These particular furnaces are a popular option and we keep them in stock and ready for immediate shipment.
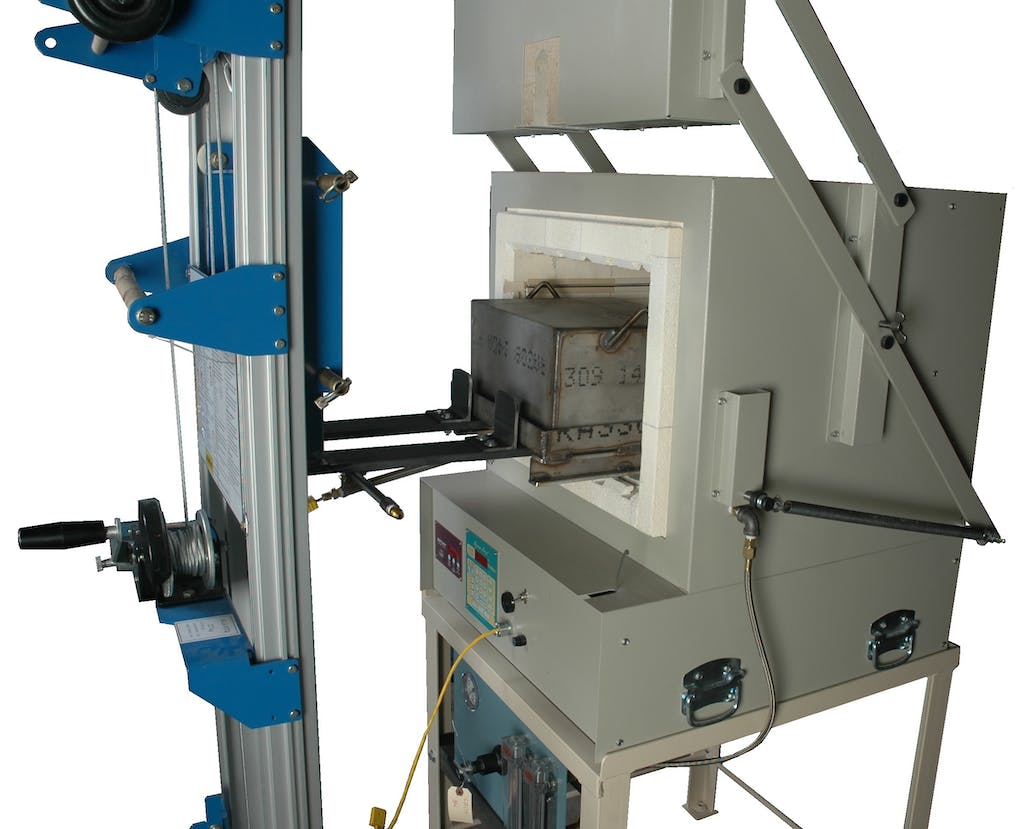
Model GS1714R with inert atmosphere retort and optional loader.
At L&L Special Furnace Company, we have a reputation for quality and value that has enabled us to provide industrial ovens, furnaces, and quench tanks to customers in industries where precision, quality, and reliability are critical. Regardless of your industry – aerospace, oil & gas, manufacturing, energy, medicine, or consumer products – you can contact us today to find the heat treatment solutions and customer service excellence that you need!