The National Fire Protection Association (NFPA) is an organization that promotes fire, electrical, and other hazard safety. One of the ways in which they promote safety is by setting guidelines for manufacturers to follow. The NFPA 86 guidelines are a set of standards for industrial ovens and furnaces. All L&L furnaces comply with the latest edition of the NFPA 86 guidelines.
Furnace Designs
One area that the NFPA 86 guidelines lay out is how furnaces should be designed. These design guidelines can be grouped into four main categories: structural, service, heating, and cooling.
On the structural side of things, supports must be able to support the furnace and work objects even at maximum operating temperatures and conditions. Radiation and refractory shields must also be firmly held in place. And observation ports or other visible means of observing the burners must be present. For service, the furnace must be designed so that access is provided to all parts that may require maintenance or inspection. As for heating, components exposed to high temperatures must be made from non-combustible materials. And external parts of the furnace that are hot must be guarded to prevent operator injury. Finally, critical cooling systems must be labeled and able to function even if the power fails.
Safety Labels
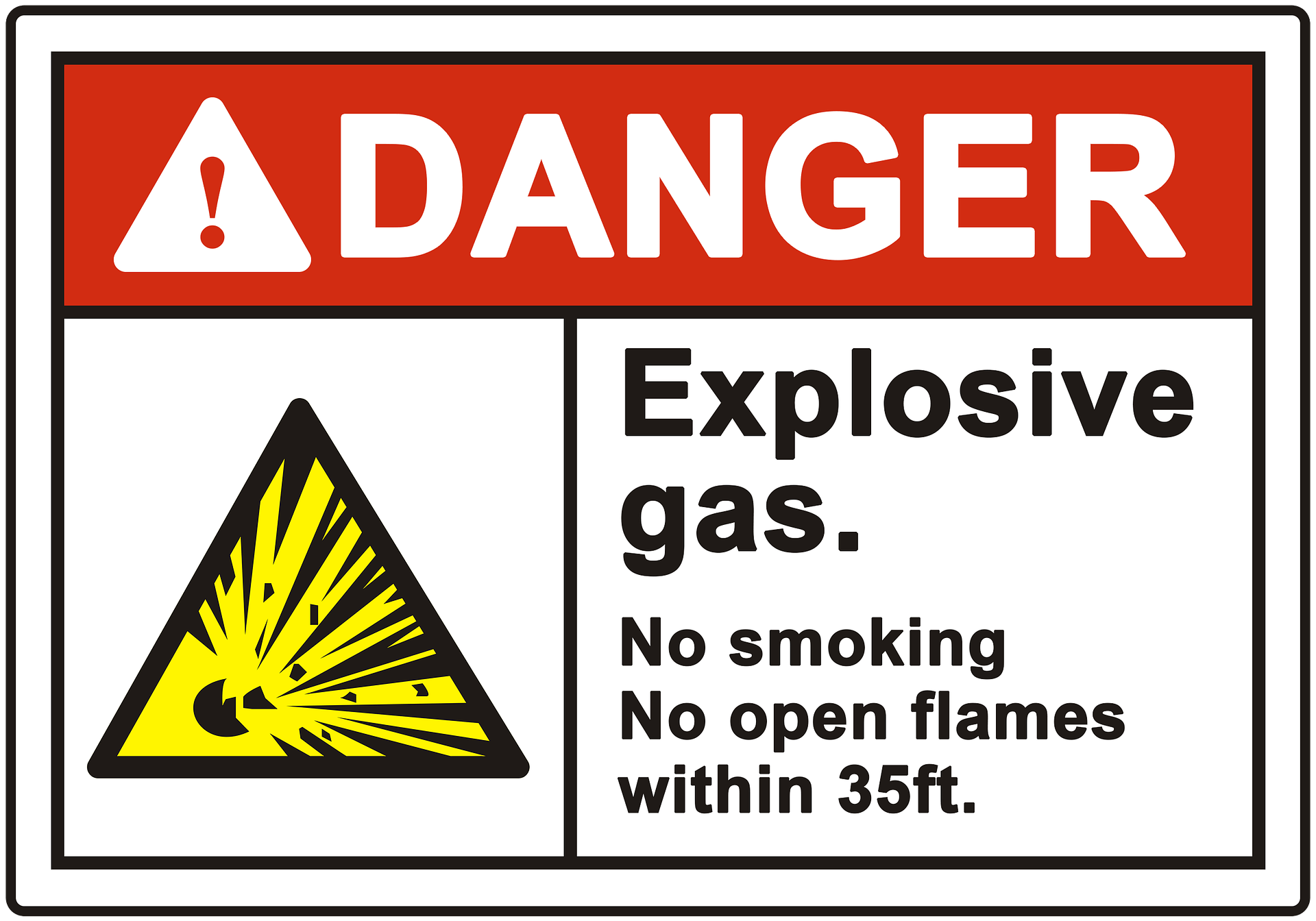
Critical cooling system labels are not the only labels required by NFPA standards. There also must be a nameplate that states the operating of the furnace. This nameplate must be accessible to the operator. Additionally, a warning label must be attached either to the furnace itself or the control panel. This label should clearly explain the operating and maintenance instructions.
Safety Equipment
As safety is the primary concern of the NFPA, it should come as no surprise that there are standards for the placement and operation of safety equipment on the furnace as well. In general, safety devices should be protected from damage and should not be able to be bypassed by either electrical or mechanical means. And, there must be at least one manual emergency shutdown switch to power off the furnace.
Additional safety features include that vents should be designed so that they do not expel heat towards operators. That would be an obvious safety hazard considering the temperatures these furnaces reach. And finally, if a programmable Logic Controller system is installed on the furnace, access to this software must be restricted to only the essential workers, such as maintenance personnel.
Fire Protection
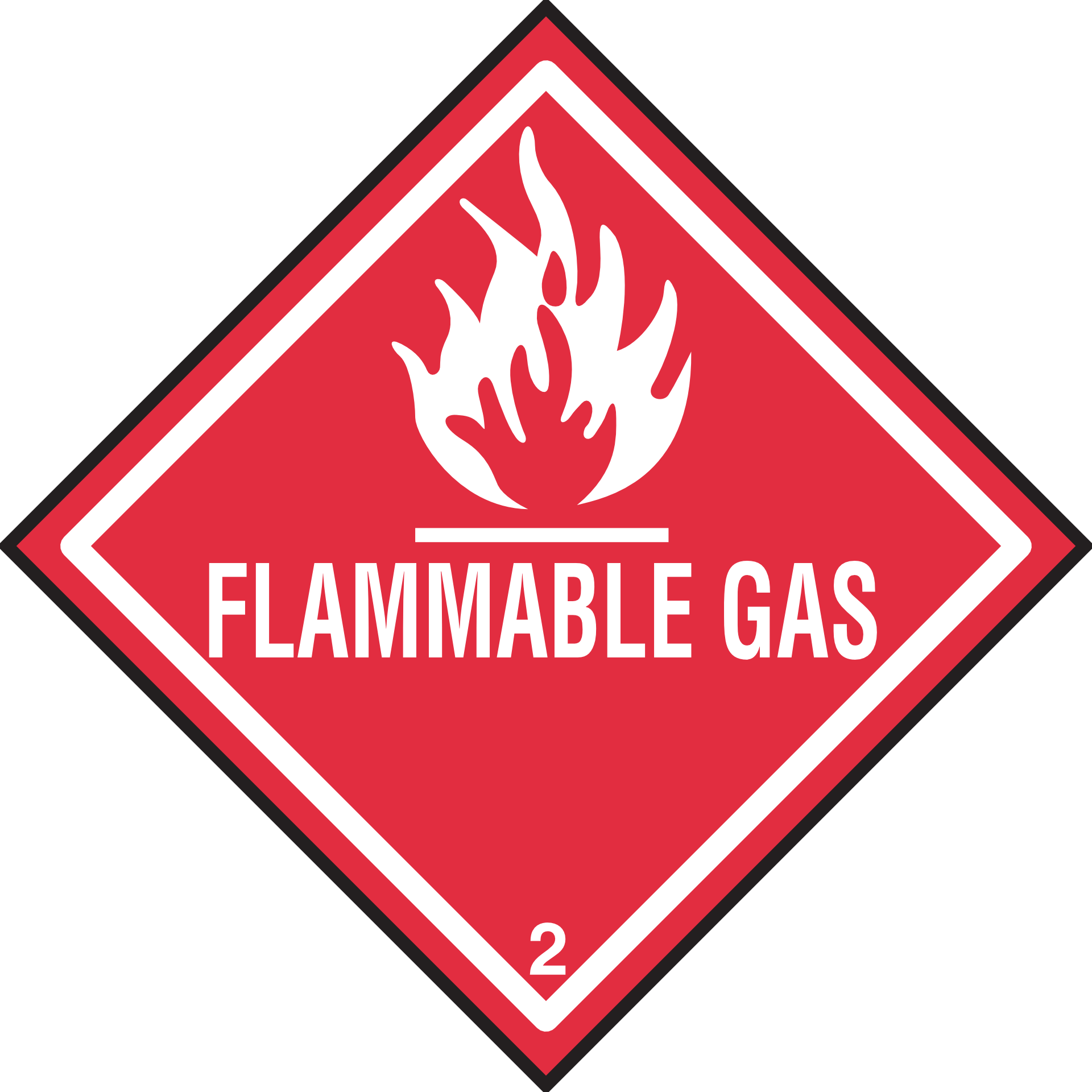
Fire protection for furnaces is fairly straightforward. Not all furnaces require fire protection. For those that do, there must be an automatic fire protection system and a manual fire protection system. The manual fire protection system simply involves doors and hatches being available and accessible. Automatic fire protection systems can take a variety of forms. Some use water sprinklers, water spray, water mist, carbon dioxide, foam extinguishers, or even dry chemicals.
Explosion Relief
Along with fire protection, furnaces also must have explosion relief vents if they have flammable liquids or gasses or combustible dusts present. Explosion relief vents are not required for low-oxygen atmosphere ovens, thermal oxidizers, or Class D furnaces (more on those in just a bit). For the furnaces that do require vents, there are a couple of rules that must be followed when implementing those vents.
First, the vents cannot be obstructed in any way because this will reduce their effectiveness at relieving explosive pressure. And again, the vents must not expose furnace operators, or anyone else, to injury. As for where they are located, the vents must be near the ignition source and be evenly distributed around it. When pressures build within the furnace, the vents should activate before the internal pressure reaches the maximum design pressure of the furnace. Finally, each vent must also have a warning sign posted on it.
Oven and Furnace Classes
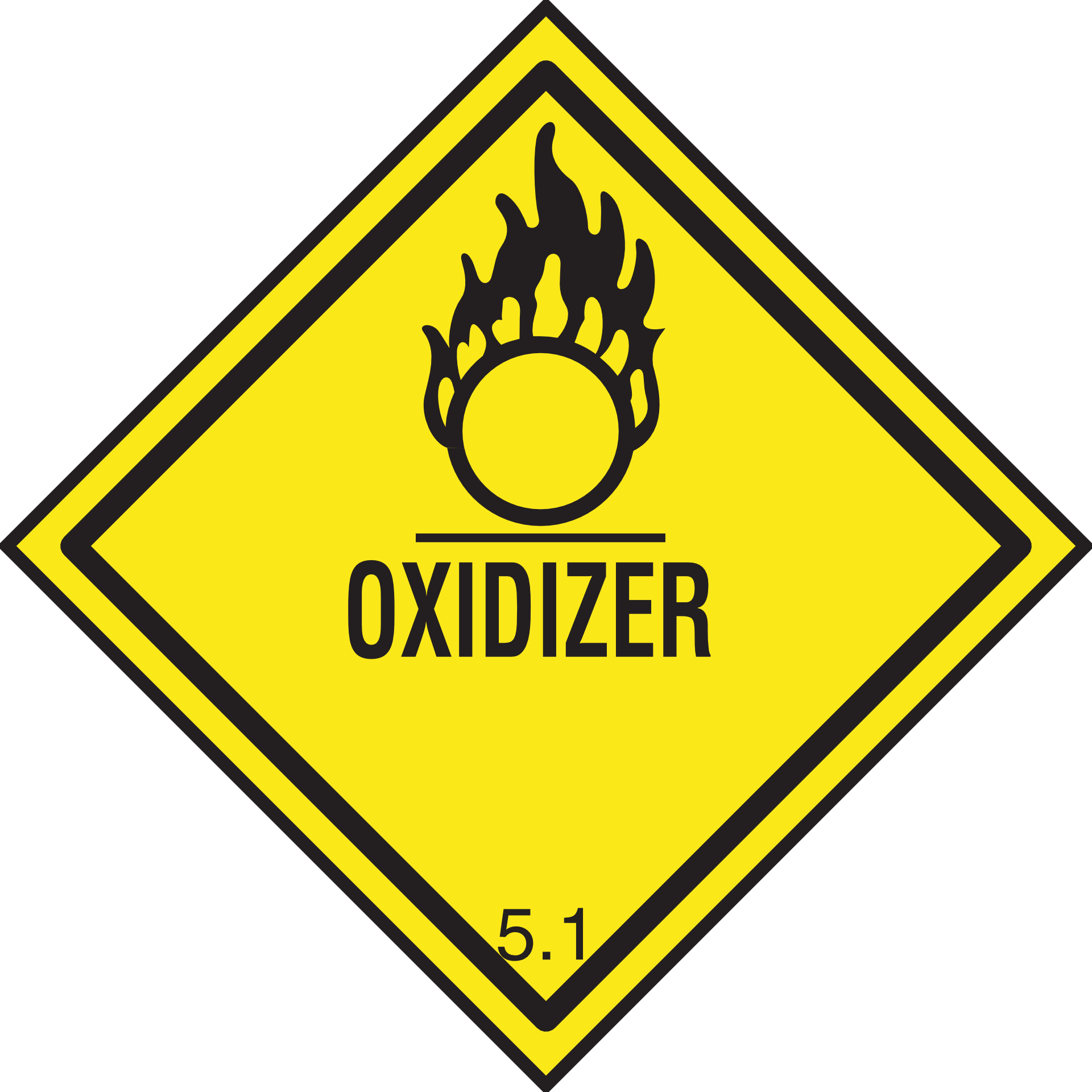
The final major section of the NFPA 86 guidelines highlights four different classes of furnace. Each class is rated for specific operating conditions and must be labeled accordingly. These classes are simply referred to as A, B, C, and D.
Class A furnaces are those that operate at approximately atmospheric pressure and have the potential for explosion or fire hazards. The explosion or fire hazards could be caused by the presence of flammable or combustible materials heated in the furnace. That means the primary basis for the Class A rating is dependent on what type of materials the furnace is meant to heat. Class B furnaces also operate at approximately atmospheric pressure. However, they are not used to heat flammable or combustible materials.
Class C furnaces differentiate themselves from Class A and B furnaces due to their use of a special atmosphere. For these furnaces, the atmosphere itself is what is flammable, not the materials being used. And Class D furnaces also have special uses. These furnaces can include special atmospheres, but that is not necessarily their defining trait. Instead, their defining characteristic is that they are vacuum furnaces. Their temperatures can also range from slightly above natural ambient temperatures to over 5000°F
Conclusion
The NFPA 86 guidelines set standards for how industrial furnaces and ovens are to be built in order to promote safety. The guidelines lay out how furnaces should be designed, labeled, and equipped in case of fire or explosion hazards. And, there are four classes of furnace that have been defined to make it easier to tell which furnace is rated for which kind of usage.
L&L Special Furnace
At L&L Special Furnace, we design and manufacture industrial furnaces for a variety of uses. With the latest edition of the NFPA 86 guidelines established, all furnaces we build meet the new specifications. Contact us today for more information on our wide range of furnace models.