Automotive heat treatment is essential for maintaining the structural integrity of modern cars. Metal components vary in type and quality, and different heat treatment methods are required for lightweight aluminum body parts, along with high-strength engine and drivetrain components.
This post will take a look at how automotive heat treatment is used for the various components in today’s cars and light trucks. It will cover the components that receive heat treatment, as well as the types of techniques that might be used.
Understanding Common Automotive Heat Treatment Techniques
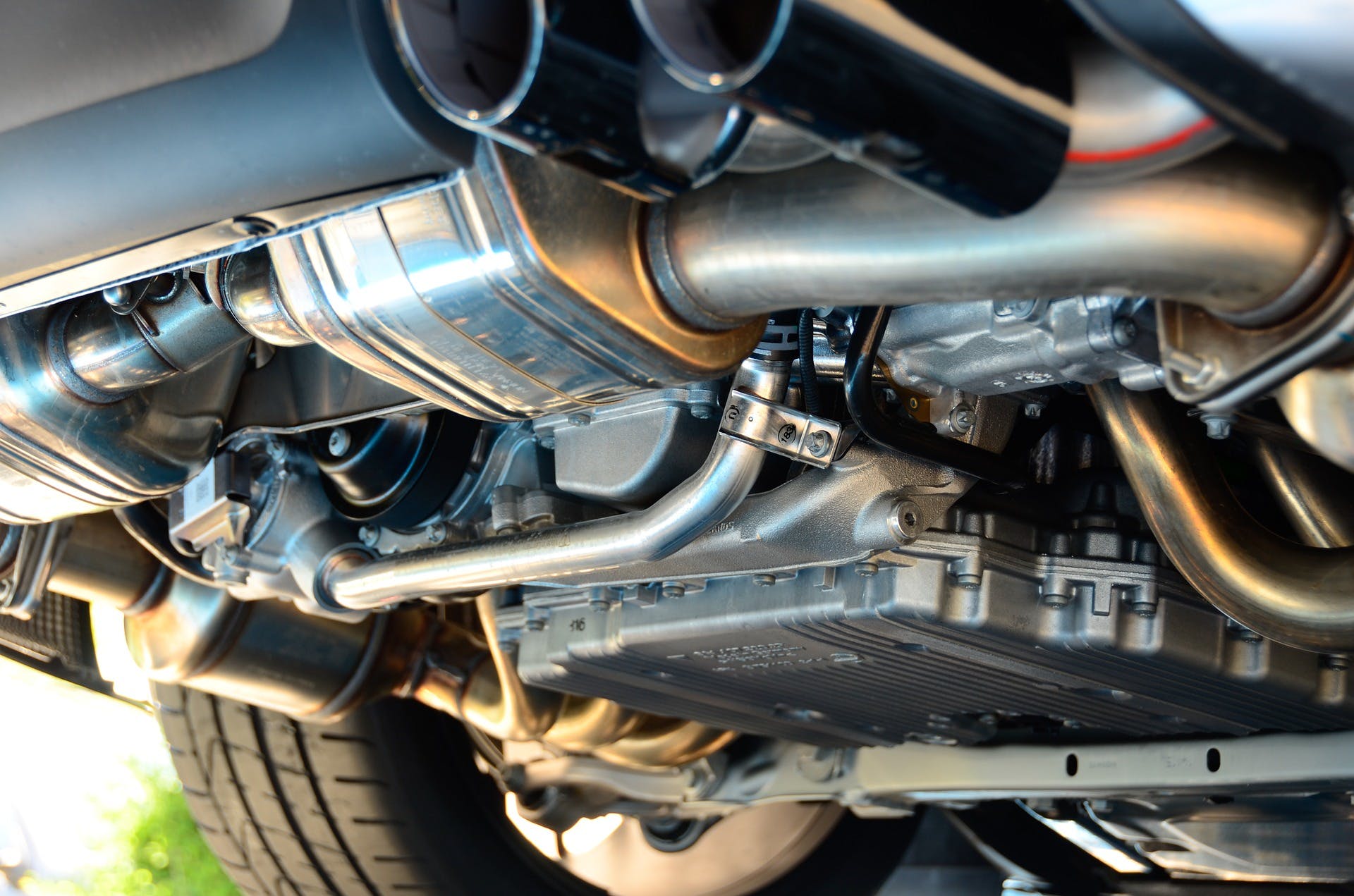
There are many types of automotive heat treatments performed in the industry. Here are some of the more common methods of application as they relate to the parts discussed below.
Hardening
Hardening is an umbrella term to describe the process of heating a metal above its critical temperature before quenching it in a medium, such as oil or water.
There are different types of hardening processes. Furnace hardening is the simplest, relying on a furnace to raise the temperature prior to the heat being quenched. But many automotive components demand attention to their specific geometric configurations, which requires a method with more finesse.
Induction hardening is commonly used in the automotive industry, as it can quickly and selectively harden the surface of metal parts. In this method, a copper coil is placed near the surface of a metal component, which allows heat to transfer to the metal. Once it is quenched, the material is significantly harder than it was previously.
Tempering
Tempering is similar to the hardening process in that a previously hardened metal is heated below the critical temperature and then cooled in air. The XLE Series of furnaces are ideal for both hardening and tempering processes.
Carburizing
Carburizing is the method by which carbon is introduced to a metal like steel. The result is a component that is both lightweight and highly durable. CB Series furnaces are purpose-built for carburizing.
A quick survey of today’s automotive heat treatment techniques will reveal a variety of methods for carburization.
Low-pressure carburization relies on a vacuum furnace, in which high heat and low pressure ensure the thorough diffusion of carbon atoms in the steel.
Gas carburization heats the metal in a carbon-rich atmosphere, often relying on a carrier gas that’s high in hydrocarbons. This allows carbon to diffuse throughout the metal.
Ferritic nitrocarburizing relies on carbon, nitrogen, and heat to improve the durability of a metal component.
Nitriding
Nitriding is the process of introducing nitrogen to the surface of a metal to create case-hardened steel. In the automotive industry, this process tends to be applied to low-alloy steel, as well as aluminum and titanium components.
Carbonitriding
Carbonitriding is similar to nitriding, though both carbon and nitrogen can be applied to a metal’s surface to increase its strength.
Applications of Automotive Heat Treatment
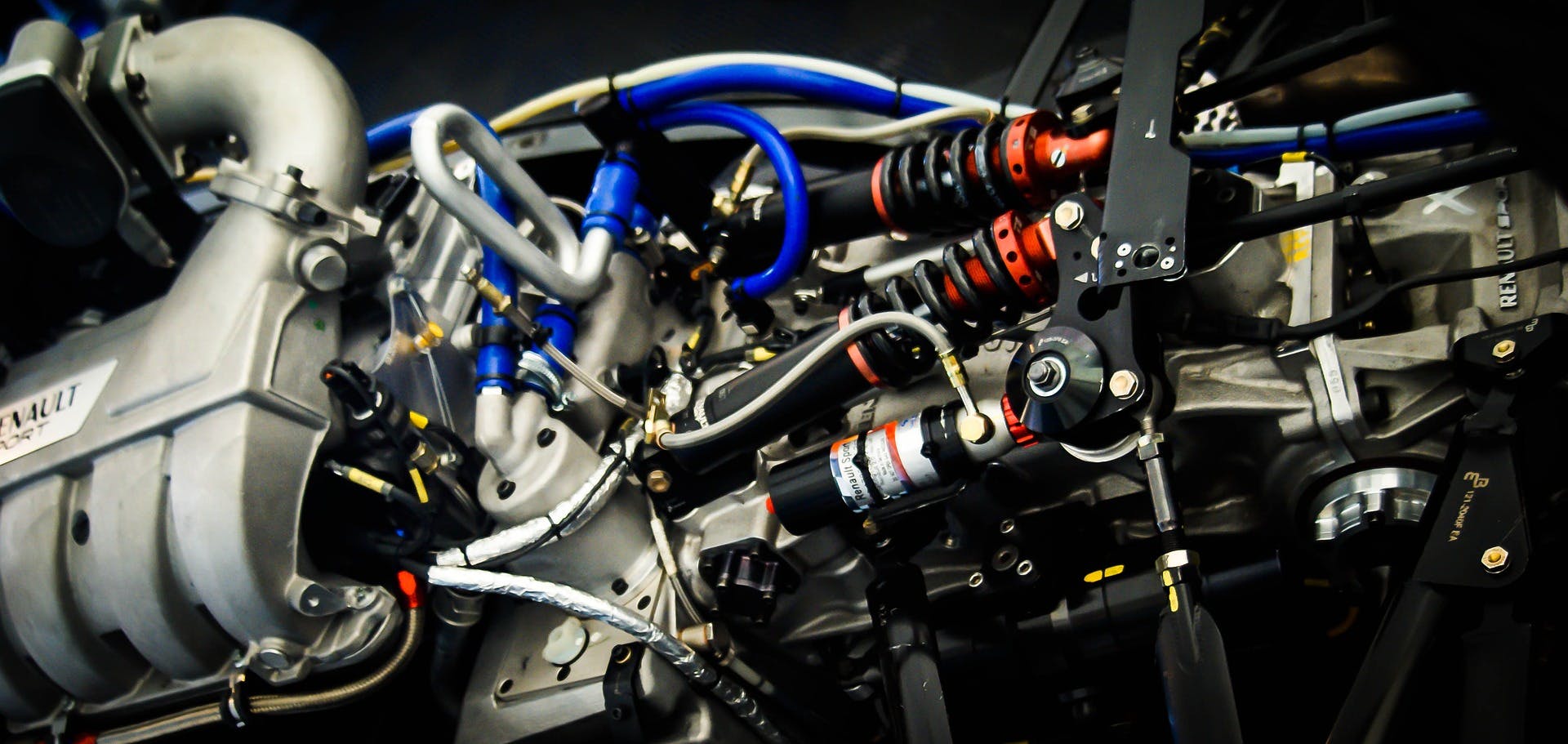
Now that you understand some of the common techniques, we’ll take a look at the parts that typically receive heat treatment.
Engine and Powertrain
The components of your engine and transmission have to withstand high temperatures, corrosive chemicals, and the ever-present wear and tear that come from normal engine operation.
Automotive heat treatment can improve the durability of critical components, including:
- Shafts
- Retainers
- Hubs
- Pinions
- Gears
- Support arms
- Pistons and valves
At the same time, the highly sensitive nature of these components necessitates specific types of automotive heat treatment processes. Gears, for example, must be heat-treated without compromising the geometry of the gear tooth.
Powertrain components are typically treated with one of the following methods:
- Induction hardening
- Low-pressure carburizing
- Gas carburizing
- Ferritic nitrocarburizing
- Carbonitriding
Induction hardening can be particularly effective at hardening components such as gears without altering their unique geometric properties.
Wheels and Drivetrain
The drivetrain does the bulk of the “heavy lifting,” so to speak. The load-bearing elements of a vehicle’s drivetrain must be strong and durable.
These elements include:
- Gears
- Differential case and pins
- Axle shafts
- Friction plates
- Hub annulus
These components are treated for strength. As with the engine, certain parts must also retain specific geometric configurations to retain their utility.
Common automotive heat treatment methods include:
- Induction hardening
- Furnace hardening
- Carburizing
- Ferritic nitrocarburizing
In some cases, the manufacturer’s choice of material will govern which heat treatments are necessary to improve the overall integrity of these parts.
Brakes
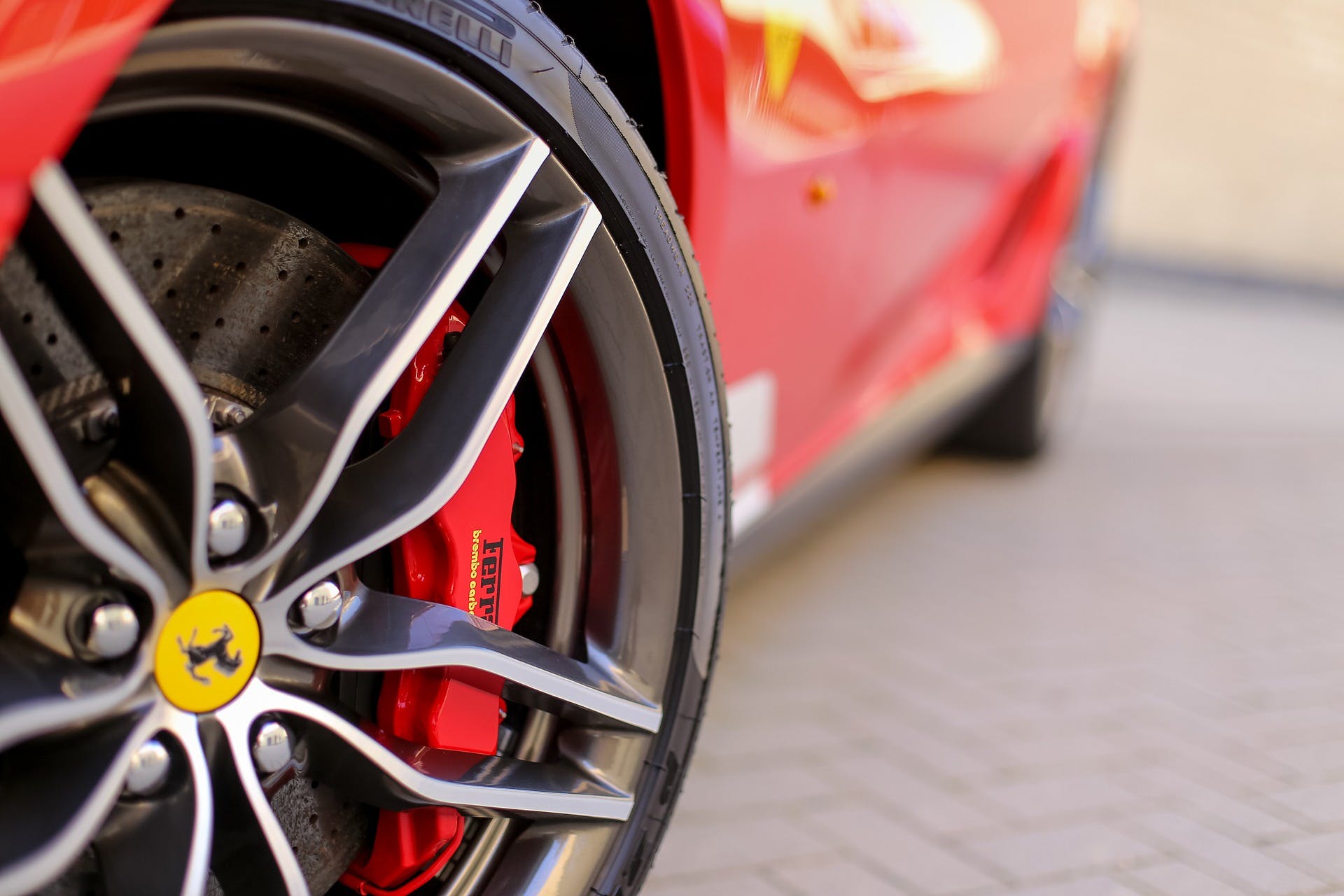
Brake systems are especially vulnerable to wear and corrosion. The hydraulic brake fluid included in a typical brake system can contribute to the deterioration of the components of a brake system, which already have to regularly endure high levels of stress from repeated use. Additionally, the overall safety of the vehicle — and its passengers — depends on the structural integrity of the brake system.
Typically, the following brake components receive heat treatment:
- Brake web
- Caliper piston
Additionally, the various stampings in the braking system may receive heat treatment. Typically, the following hardening techniques are used:
- Induction hardening
- Nitriding
The manufacturer’s choice of components may influence the automotive heat treatment method used, and some may use other case hardening techniques to achieve a specific result.
Chassis, Suspension, and Steering
Automotive heat treatment is essential for the exterior and suspension of a vehicle. The suspension and steering components demand high resistance to wear and corrosion since these parts are the most exposed to the weather, as well as chemicals and debris on the road surface itself.
Heat treatment is used to ensure the integrity and durability of these essential elements, which include:
- Seating
- Ball studs
- Torsion bars
- Arm lever
- Pins and fasteners
It’s not uncommon for some manufacturers to attempt to minimize costs by utilizing less expensive steel. There’s nothing wrong with this, though this may require greater attention to the heat treatment process.
Typically, these components are treated using one of the following techniques:
- Induction hardening
- Ferritic nitrocarburizing
- Continuous furnace quench and tempering
These processes ensure the durability of the components, which ensures that drivers retain full control over their vehicles.
Automotive Heat Treatment Requires Specialized Equipment
The type of heat treatment technique used depends on the material and component being treated. Induction hardening, for example, can be used to harden sections of a metal part without altering its geometric properties, like the teeth on a gear. For performing a variety of heat treatments on aluminum components, the DRQ and ADC Series are great options.
L&L Special Furnace Co., Inc. has a history and reputation for excellence in the heat-treating industry. Contact us today for more information about our furnaces and for help selecting the right one for your needs.