Both batch processing and flow control are important terms to know if you are involved in the manufacturing industry. The furnaces created by L&L Special Furnace are crucial to this industry at large. Once a part is fabricated there are extra steps which often need to be taken, such as thermal processing. This thermal processing of parts is more common than most would think. And there are two ways to go about thermal processing: batch processing, which relies on flow control, and mass production.
What is Flow Control?

Before we can dive into batch processing and mass production it is important to understand what flow control is. After all, flow control is the main factor which sets batch processing and mass production apart.
You can think of flow control like supply and demand. The need for specific parts controls the flow of production. For example, if there is a high demand for part A, a low demand for part B, and no demand for part C, flow control dictates how much of your time and resources are put into creating each type of part. In this example, part A would receive more time and resources than part B, and part C would receive little to none.
A good way to differentiate flow control from supply and demand is the focus each takes in maximizing profits. Supply and demand typically focuses on expanding the supply to match demand, thereby increasing profit. On the other hand, flow control typically focuses on reducing costs such as wasted time and resources, thereby increasing profit.
Batch Processing vs. Mass Production
In many ways, batch processing and mass production are opposites. What one does well, the other typically does not. Luckily this means it is fairly easy to determine which system of production you should be using for any given process.
Batch processing excels in situations with a relatively low (compared to mass production) number of parts which need to be processed. For situations in which the parts being processed may change rapidly, batch processing is also the preferred method. Some aspects of batch processing furnaces include:

- Lower overall costs due to non-continuous operation
- Higher costs per individual part because they are “specialized”
- Limited scaling capabilities
- Minimum overstocking of inventory because parts are processed “on-demand”
- Usefulness for research and development due to less overall cost and time
Mass production excels in situations where there is a high, never-ending demand for a part to be processed. However, while mass production is great for large numbers of similar parts, it is not suited for changing demands. Some aspects of mass production furnaces include:
- Higher overall costs due to continuous operation
- Lower costs per individual part because they are not “specialized”
- Near infinite scaling capabilities
- Excess stock of inventory because parts are processed regardless of demand
- Lack of research and development potential due to the process being streamlined
However, while batch processing and mass production furnaces each have distinct advantages, that does not mean they are mutually exclusive. In many cases it is beneficial to have both types of furnaces. Mass production furnaces will allow you to churn out large quantities of parts you know will be in demand. But batch processing furnaces will allow you to test new parts before they are mass produced and thermal process smaller quantities of more specialized parts.
Uses for Batch Processing Furnaces
L&L batch processing furnaces have been used to develop manufacturing practices for a wide variety of industries. These industries often rely on more specialized parts which the mass production method would not work well for. Batch processing furnaces are used for:
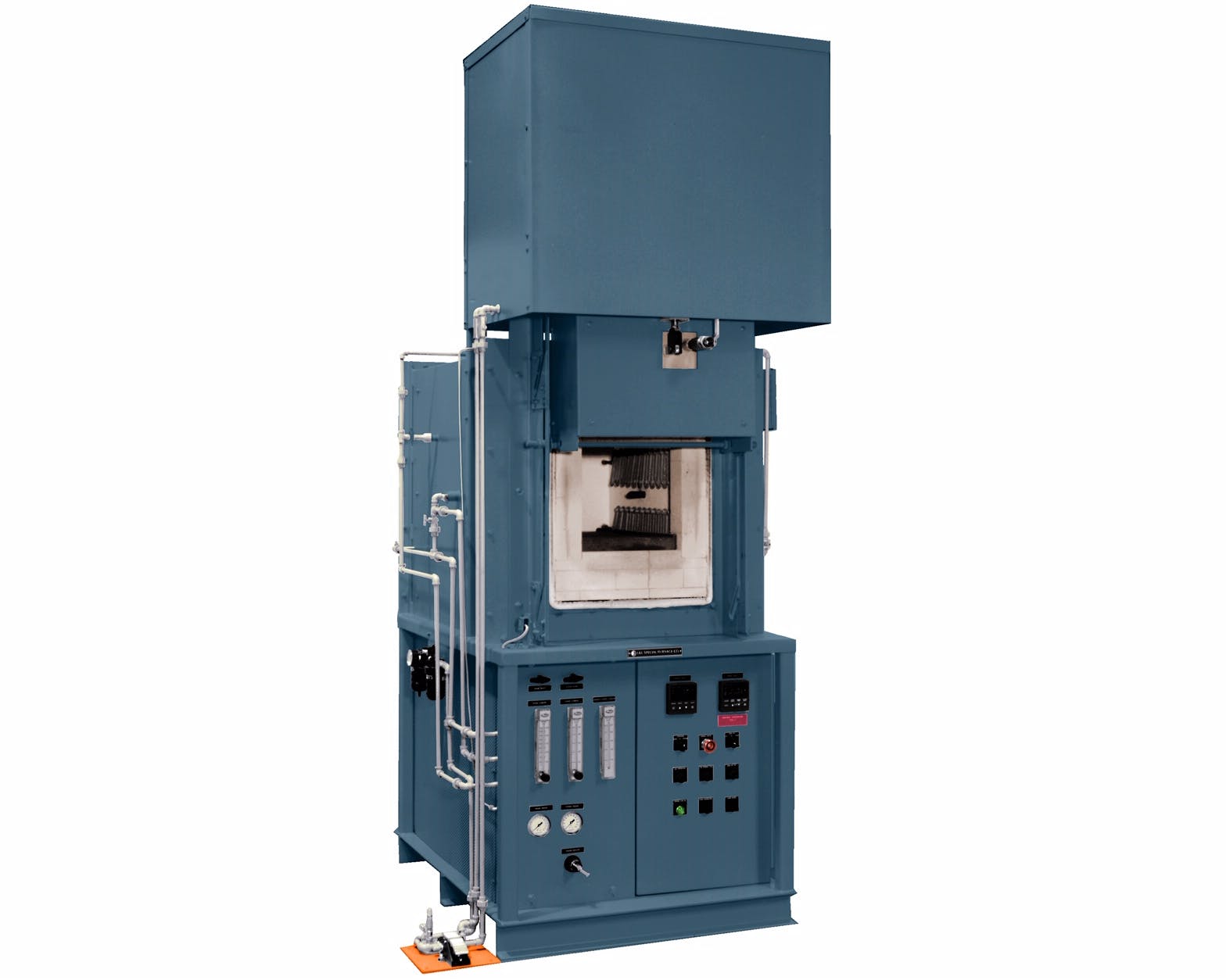
- Glass slumping for telescopic lenses
- Annealing of optical lenses
- Sintering of medical grade powders
- Ceramic matrix composites
- Nuclear magnetics & particle acceleration
- Curing of dental appliances
- Medical implant devices
- Various military & defense projects
In the cases of telescopic and optical lenses, dental appliances, and medical implant devices each part is highly specialized, which makes batch processing the perfect method of thermal processing. The nuclear magnetics, particle acceleration, and military fields rely heavily on research and development. In these fields, small quantities of parts need to be processed, tested, altered, and processed again until a final product is settled on. Other uses for batch processing furnaces are for products that, while not necessarily specialized, are not in very high demand.
Conclusion
Batch processing and flow control are intrinsically linked together — flow control is the guiding force of batch processing. And in a different sense, batch processing and mass production are linked as well due to the two methods of thermal processing covering each others’ weaknesses. But while mass production is often viewed as the pinnacle of manufacturing from an outside perspective, many industries rely on the batch processing method of thermal processing for integral parts.
Batch Processing with L&L Special Furnace
L&L Special Furnace has been supplying standardized and custom batch processing furnaces to manufacturers in a variety of industries for many years. Our furnaces are ideal for any start-up or pilot plant that will be using research and development methods to develop a thermal process. And even for companies which plan to go into mass production, our batch processing furnaces are integral for refining your process before expanding your output. Contact L&L Special Furnace today to learn more about our state of the art batch processing furnaces.